Warm Welcome to OPEX MENA
Launched in 2013, OPEX MENA is a high-level and interactive annual forum, that helps organisations in the MENA region to share the current thought leadership approaches and advanced methodologies for improving performance through strategies related to operational excellence and safety.
OPEX MENA - a unique event where over 80% of attendees are key specialists and executives from downstream producer companies.
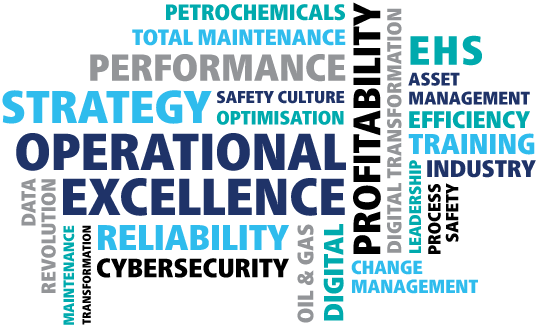
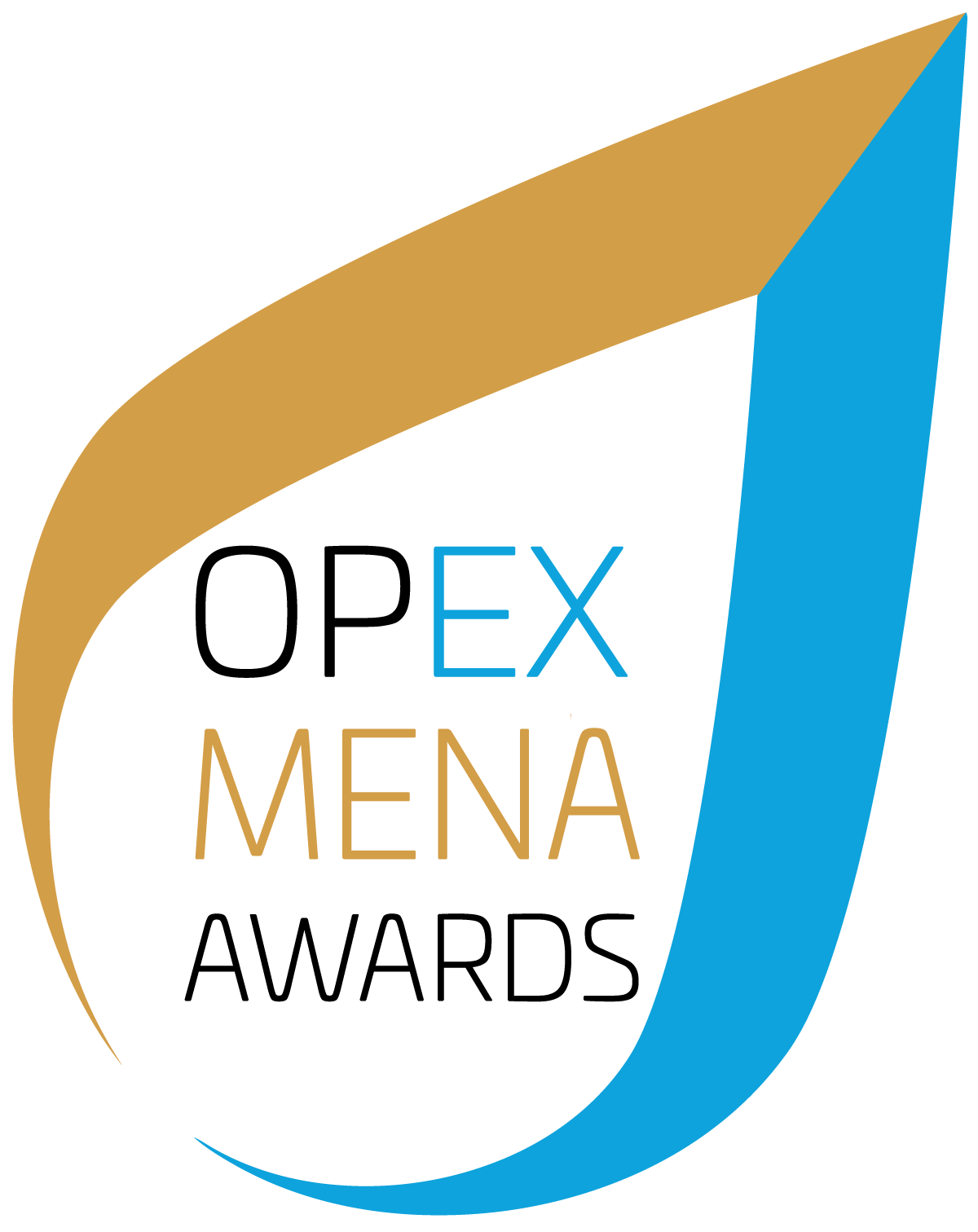
OPEX MENA AWARDS
Recognising and Rewarding Outstanding Achievements
Following the overwhelming feedback we received from the people who have made this great event the success it is today, OPEX MENA has increased the number of Awards Categories to recognise and reward a broader scope of the exceptional talent, both organisational and individual, that exists within the region’s Operational Excellence and HSE communities.
By sharing the examples, and showcasing the achievements of the OPEX MENA AWARDS winners, we hope to drive innovation and change, promote best practice, and help shape a better future for our region.
Safety Award • Operational Excellence Award • Innovation Award •
Woman of the Year • Young Professional of the Year
Latest Insights
Exclusive first-hand insights, reports and interviews at the pulse of the global oil and gas downstream industry
BLOG ARTICLE
January 2023
From Good to Great: Transforming Your HSE Performance
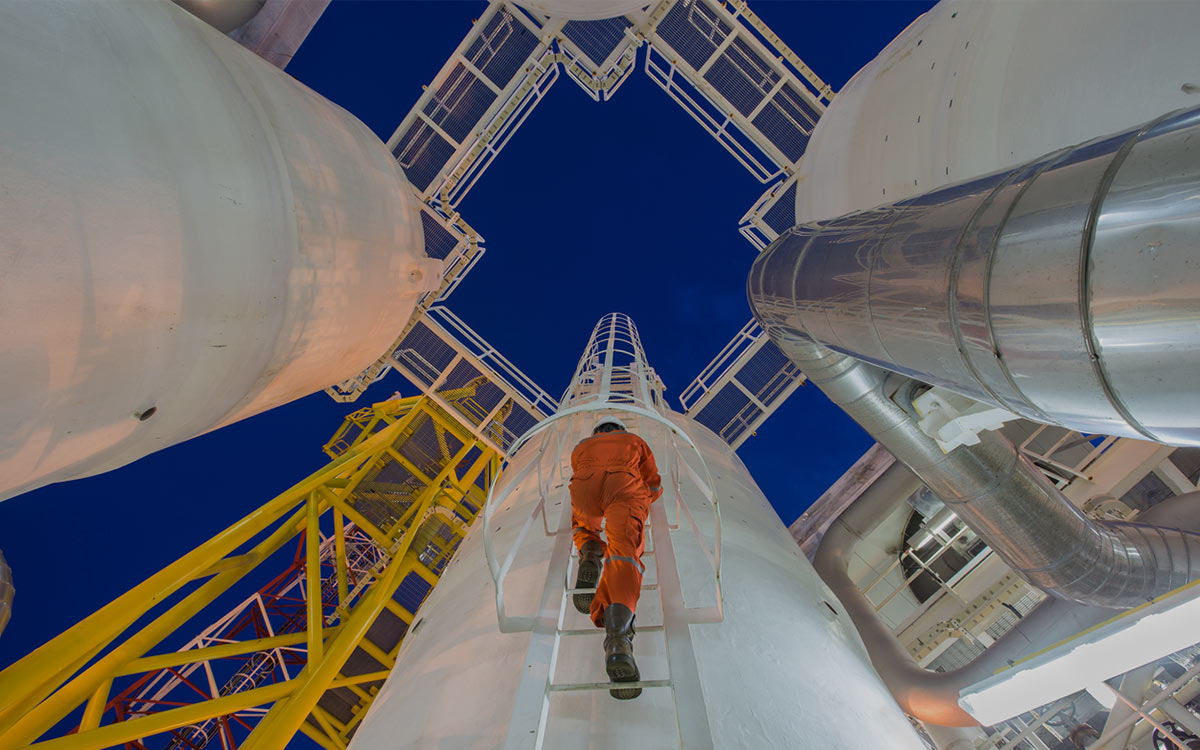
Achieving a real transformation in health, safety and environmental performance is a challenging task that requires a thorough understanding of an organisation's current HSE performance ...
Read ArticleBLOG ARTICLE
November 2022
Leadership Competency & Visibility: the Key Ingredients for a Healthy Culture
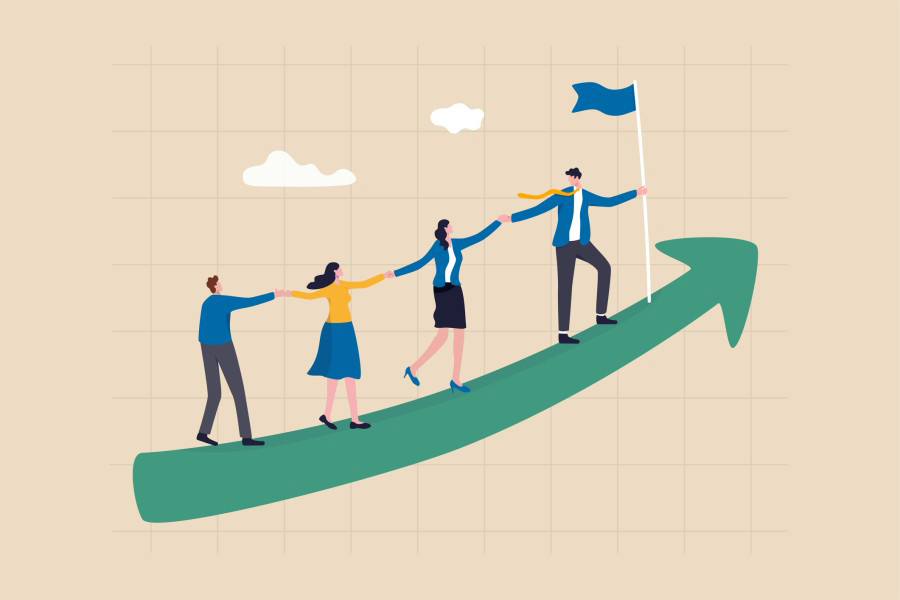
Regional operators have reached 37 million man-hours, fast approaching 38 million, without a TAR and they have not had a major incident, or accident involving contractors, or employees ...
Read ArticleLeadership Competency & Visibility: the Key Ingredients for a Healthy Culture
OVERVIEW OF THE CURRENT HSE STATUS IN MENA REFINERIES
Regional operators have reached 37 million man-hours, fast approaching 38 million, without a TAR and they have not had a major incident, or accident involving contractors, or employees since the beginning of the century. The main focus of their HSE philosophy is honesty.
Due to their processes, plants generate a lot of CO2, but there is the need of complying with the 2030 net zero targets and most plans nowadays have their own net-zero strategies in place. As an example, one regional Methanol and Ammonia plant used to emit all of the CO2 was emitted into the atmosphere, but then in 1998, they began to produce urea which, only 13 years later was utilising the majority of the CO2 produced, and with the introduction of MHI technology, they are also capturing the carbon from their flue gas now.
Since 2012 ESG has been a key focus area and many refineries now publish their sustainability report. Operators are already meeting 80% of their requirements and they engaged somebody to conduct a gap analysis and implement an ESG framework. They have just had CAPEX approval to implement a new digitalisation platform to improve OE and HSE. They have connected their Distributed Control Systems (DCS) and are analysing safety and field data to improve operational efficiency.
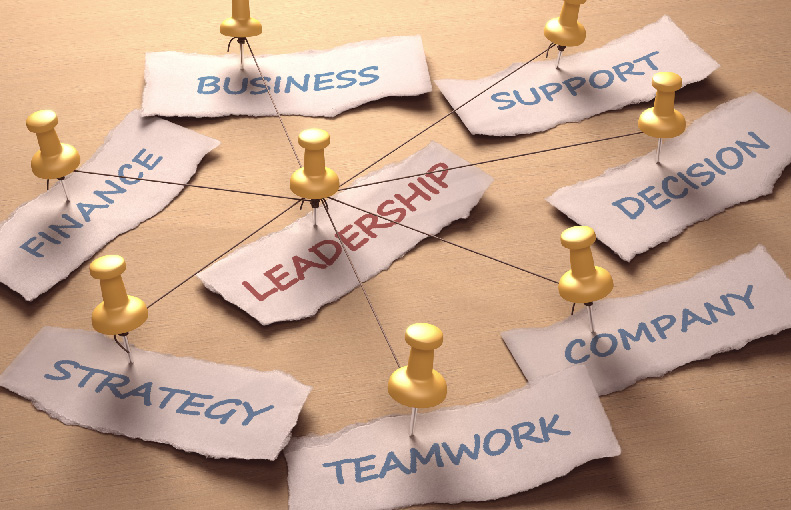
Another focus area is the loss of competency and the high proportion of young engineers. Culture plays a big role. Many companies are actively trying to integrate young professionals into the existing organisational culture, but at the same time, encouraging them to have their own ideas that will contribute positively to improving the culture.
In other regional refineries, leadership accountability and engagement are at the core of their OE system. Leaders must be visible in the plant and this regional operator mandates that their leaders conduct regular site visits in their areas of responsibility - these visits are tracked and reported to the OE and HSE teams. They instil a Positive Practice Engagement culture - if a leader sees something positive, they encourage it, which is referred to as Positive Capturing. Many have in place a good digital platform to capture these positive practices, which are tracked as KPIs and audited to determine the effectiveness of the activities and engagement.
For yet another regional refinery, the leadership focus is a passion. As they see it, the important aspect of leadership is having the appropriate leadership competency at all levels; frontline, mid and senior executive levels of the ladder. Most leadership skills are not inherent, they are learnt. As a result, this operator puts a lot of effort into creating initiatives to develop leadership skills. For example, they have a weeklong bootcamp for frontline downstream leaders. They bring 24 leaders together at one time for a safety leadership forum and they conduct 12 such events each year. Leadership forums are hosted by the local managers, endorsed at the corporate level and external speakers are invited.
The Leadership Pyramid model demonstrates five essential levels that every leader should be aware of: at the bottom - the mission, vision, and values that are ingrained in the organisation. At the next level - a hazard-free workplace where risk is effectively managed. Then - a management system that is effectively implemented within the organisation. Then the workforce - that they are fit for duty and informed about the importance of safety. They need education, understanding, and buy-in to make this part of their culture and finally, at the top level, is leadership. Leadership is responsible for ensuring all 5 levels work effectively. A lot of responsibility and accountability is placed on frontline managers, so it is important they are provided with competency development opportunities and that they are regularly assessed to determine their level of competency and to identify and address any gaps.
Leadership accountability and engagement are at the core of the OE system
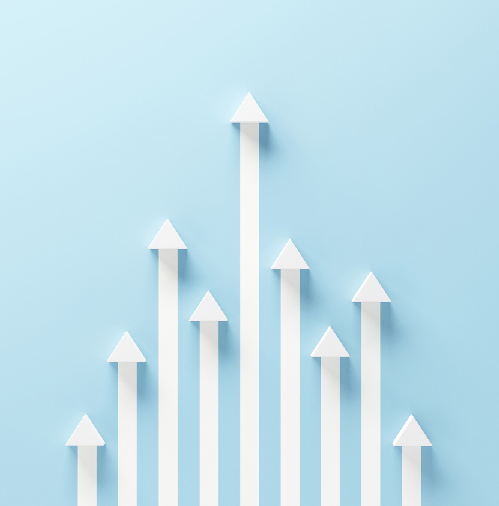
Leadership is fundamental and crucial for success and giving the frontline manager responsibility is paramount. It is the frontline manager who is sent to the shop floor. This person must deliver the right message, and it is important the right message has been cascaded down. Visible, effective leadership comes from different levels and departments being on the same page, knowing what to focus on and what message to share. An aggressive and diminishing management style will destroy the safety culture. Sending the right message, in the right way and having a clear, collective vision that is communicated through a uniform message from various levels, is fundamental.
Visible, effective leadership comes from different levels and departments being on the same page, knowing what to focus on and what message to share
Operators in the region are putting a lot of effort into creating initiatives to nurture talent and develop leadership skills. Based on the overwhelming feedback we have received, OPEX MENA AWARDS has increased the number of Awards Categories to recognise and reward a broader scope of the exceptional talent that exists within the region’s Operational Excellence and HSE communities, including “the Young Professional of the Year” and "Woman of the Year".
This article is part of the OPEX MENA Advisory Committee Report. If you have enjoyed the piece and wish to read more, downlad the full report here.
From Good to Great: Transforming Your HSE Performance
Achieving a real transformation in health, safety and environmental performance is a challenging task that requires a thorough understanding of an organisation's current HSE performance, management systems and culture. Without these key components, it is difficult to develop an effective "call to action," understand the root causes of problem areas and create a targeted action plan to transform performance.
Procyon Group has developed a four-step methodology to drive such a transformation, as shown in Figure 1.
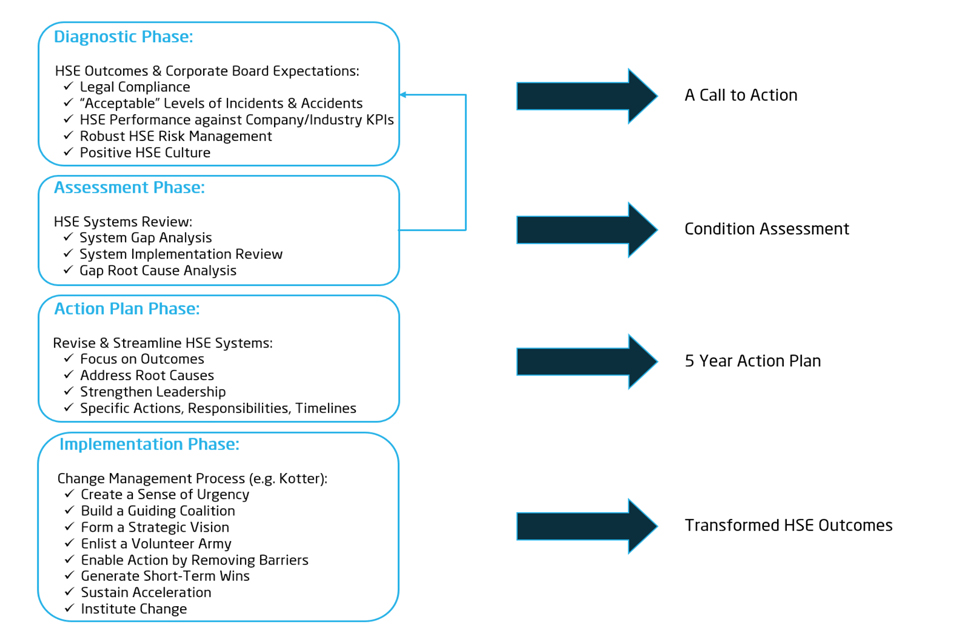
Figure 1 - Procyon Group's four-step methodology
Step 1: Diagnostic Phase
The Diagnostic Phase entails an analysis of existing HSE outcomes, which is critical for articulating a "Case for Change" and identifying areas for transformation. This analysis includes the following typical Corporate Board expectations of a high performing organization.
- Legal compliance: ensuring compliance with relevant laws and regulations is essential.
- “Acceptable” levels of incidents and accidents: analysis of incident and accident data provides invaluable insights into the root causes of problems and identifies patterns and trends that must be addressed.
- HSE performance against company/industry HSE KPIs: by comparing an organization's HSE performance to industry benchmarks and it’s own KPIs it is possible to identify areas where the organization needs to improve.
- Robust HSE risk management: identifying and evaluating the organization's most significant HSE risks is crucial for developing an effective action plan.
- Positive HSE culture: a thorough assessment of the organization's HSE culture provides invaluable insights into the attitudes/behaviours of employees and identifies areas to strengthen.
The outcome of the Diagnostic Phase is an assessment of HSE outcomes being delivered by existing HSE systems and, where performance is sub-standard, a “Case for Change” to engage with leadership and incentivise the transformation.
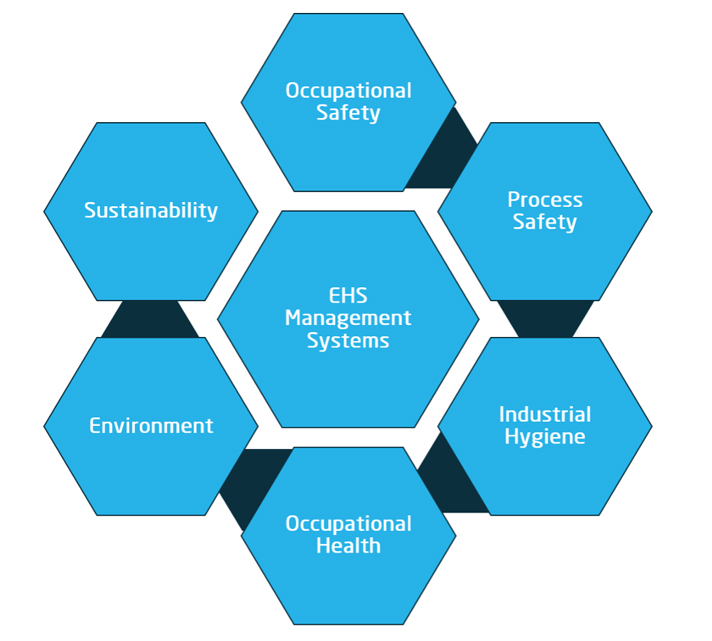
Figure 2 - Assessment Phase - review system and technical topics
Step 2: Assessment Phase
The Assessment Phase entails a comprehensive review of the organisation’s existing HSE and associated management systems and their implementation across the organisation.
To facilitate this review, Procyon Group utilise "Insight", an integrated framework app which uses a systems maturity assessment approach to deliver a systematic, comprehensive and clearly communicated systems review. Root causes of any shortfalls are also identified.
The scope of the review is company-specific, but can include the following systems and technical topics, as per the image below:
The assessment is made against established criteria that reflect a progression from “Nothing In Place”, through various levels of systems development/implementation, to “Best Industry Practice”.
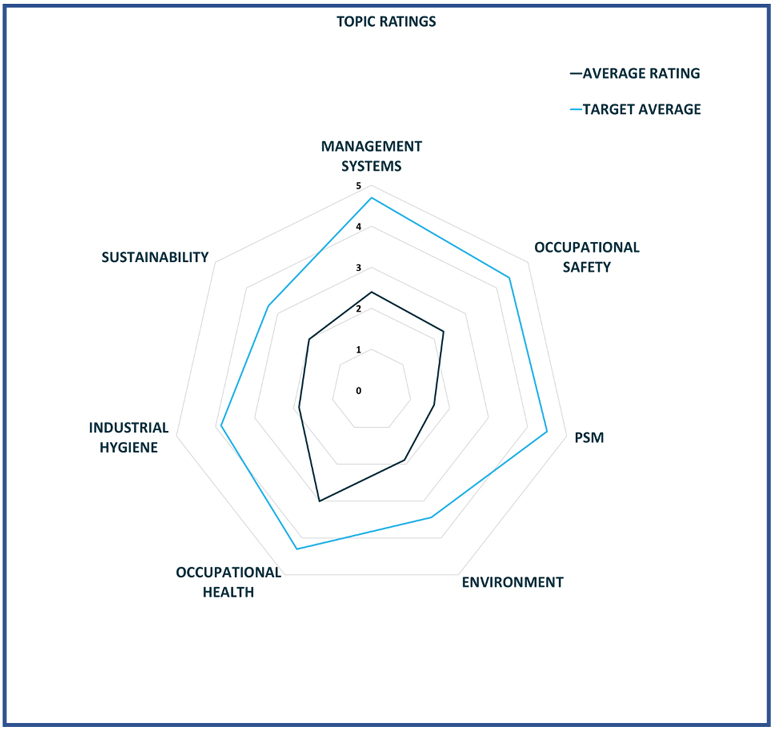
Figure 3 - Assessment topic ratings
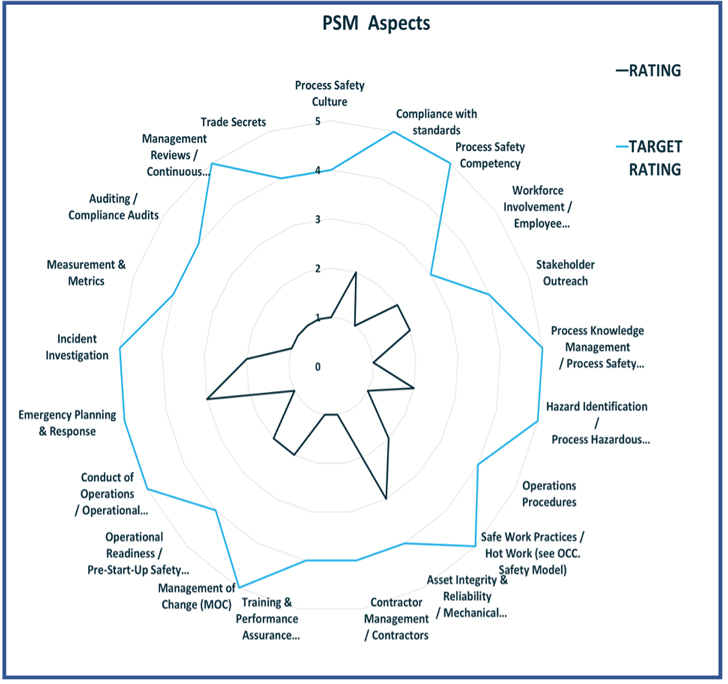
Figure 4 - PSM Aspects
The scoring of systems maturity, along with company ambitions regarding the HSE outcomes it wants (i.e. Targets), allows the main gaps to be readily identified and gap closure to be tracked over time.
Step 3: Action Plan Phase
With the data and insights gained from the above assessment, a detailed and wide-ranging action plan can be prepared that focuses on addressing root causes, strengthening the organization's HSE culture and building effective, outcomes-focused HSE management systems.
The Action Plan should include specific Tasks, Priorities, Responsibilities, Target Completion Dates and Resource Requirements (e.g. CapEx/OpEx, personnel, training, etc.) As such, it needs to be prepared in close coordination with senior management, as the company’s ambitions will drive resource allocation and, therefore, the Action Plan timeline. Successful and sustainable transformation takes time and a 5 Year Action Plan is typical.
Step 4: Implementation Phase
There is so much more to the Implementation Phase than simply working through the Action Plan. It is essential that company leadership recognises that transformation is a Change Management exercise and there is no standardised approach. The Action Plan and its implementation must be bespoke to the organization.
There are many change management frameworks available. A classic example is Kotter’s 8 Steps for Leading Change, which is summarised below.
- Create a Sense of Urgency: Draw upon the Diagnostic Phase outcomes to frame the transformation that is required, why it is required and why it is required now!
- Build a Guiding Coalition: Leadership with visible commitment and drive is essential’ along with the right people to drive the change through the organization.
- Form a Strategic Vision: Develop and communicate a clear and compelling vision of the future.
- Enlist a Volunteer Army: Motivated and empowered people, driven by the common vision, are needed to affect the change.
- Enable Action by Removing Barriers: Whether existing systems, people or attitudes (“we have always done it this way”), these barriers need to be identified and removed.
- Generate Short-Term Wins: Quick wins demonstrate that the change is working and provide motivation and momentum for more change.
- Sustain Acceleration: Pushing through until the end goals are achieved is essential; stopping when the job is half done is not a transformation.
- Institute Change: Embed the change in the systems and culture of the organization so they are second nature and, therefore, sustained.
Using a change management framework will maximise the company’s chances of successfully implementing the Action Plan and achieving the HSE transformation being sought.
Close Article
OPEX MENA's Key Topics
NAVIGATING CHALLENGING LANDSCAPES AND BUILDING RESILIENCE AND AGILITY DURING TRANSFORMATION
- Driving Performance on Strategic Planning & Leadership
- Approaches for Aligning Senior Level Strategic Priorities and Economic Goals with Front-line Operations
- Implementation and Execution of Frameworks
- Inspiring Leadership - the Power of Passion for Motivating and Achieving High Results
- Focus on Change Management and Overcoming Resilience to Change
- Fostering a Culture of Learning and Embracing Technology Adoption
PROFITABLE CONVERSION ROUTES
- Engage and Cultivate Employees
- Prepare the Workforce for Volatility and Change
- Managing Skill Gaps & Shortages
- Workforce Retention and Talent Acquisition
- Enhancing OE Culture
HSE - MAINTAINING A HEALTH AND SAFETY ENVIRONMENT
- International Best Practice - Insight from Industry Experts
- Fostering Safety Culture - Going from Good to Excellent
- Crisis Management & Emergency Response Strategies
- Risk Management - Maximizing Production and Decreasing Costs at Acceptable Risk
ASSET MANAGEMENT AND PERFORMANCE OPTIMISATION
- Strategies for Increasing Reliability & Agility
- Maintenance Effectiveness & Efficiency
- Fine-tuning Assets for Peak Performance
- Process Units Maintenance - from Predictive to Pro-active Approaches
- Best Practices for Plant Turnaround Planning & Management
DATA DRIVEN OPERATIONAL EXCELLENCE & DIGITAL PROCESS SAFETY MANAGEMENT
- Driving Operational Performance and Productivity through Advanced Data Analytics & Big data
- AI and Advanced Analytics Tools
- Robotics and Intelligent Automation for Increasing Safety and Operational Efficiencies
- Digital Twins Supporting Informed Decisions and Driving Process Improvement & Safety
- Cloud-based Infrastructure
- Real-time Condition Monitoring and Predictive Analytics Technologies
INDUSTRY OE SUCCESS STORIES
Operational Excellence Case Studies in Downstream Oil & Gas will be accepted and prioritised. Proud of what you achieved? Share it!