5–7 May 2026
Dubai, UAE
Middle East Refining & Petrochemicals Tech Forum5–7 May 2026
Empowering the Future of the Downstream Sector
I'm Interested in ME-TECH 2026Welcome to ME-TECH
Cemented as the GCC’s premier technical conference for the refining and petrochemical industries, ME-TECH has helped to connect energy leaders for almost two decades - providing a unique platform to address the opportunities and challenges facing the downstream sector.
Unlocking the full potential of today’s assets in the Middle East requires a two-pronged approach-working existing assets harder in the short term while simultaneously transforming them into low-carbon, digitally enabled, and integrated energy–chemical hubs for the long term.
The region already has scale, feedstock, and integration advantages, but deploying the right technologies will determine how much more value can be extracted from existing assets.
As we look at the year ahead, we’re excited to organise the 16th edition of the Middle East Refining & Petrochemicals Tech Forum, and we look forward to welcoming you for three days of informative sessions, interactive panel discussions, expert seminars, and numerous opportunities to network with peers from the Middle East & beyond!
Change, adaptability, and foresight are key for all downstream producers – decisions made today will define the energy landscape of tomorrow.
Key Focus Area
Asset Optimisation
Approaches to increasing operational flexibility, optimising assets and navigating the complexities of feedstock variability and market dynamics
AI & Digitalisation Solutions
Harnessing advanced data analytics, AI, and digital twin technologies to enhance real-time decision-making and predictive maintenance
Refining & Petrochemical
Integration
Exploring new synergies to produce
high value products
Technology Solutions: Processes & Catalysts
Innovations in processes and catalysts that drive process improvements, enhance product yields, and reduce emissions
Quick Wins: Enhancing Energy Efficiency
Strategies for improving energy, operational and process efficiency in existing refineries and petrochemical facilities
Join our Esteemed Speaker Panel
We are calling for abstracts in the following areas:
- Asset Optimisation
- Quick Wins: Enhancing Energy Efficiency
- AI & Digitalisation Solutions
- Technology Solutions: Processes & Catalysts
- Refining & Petrochemical Integration
Case studies and practical examples of technology application and implementation will be favoured!
Highlights from the Last Edition
Thank you to all our incredible speakers, panellists, sponsors, exhibitors and delegates who made our ME–TECH 2025, a real success! The support and discussions that took place have been truly inspiring and we look forward to continuing our journey together.
We hope to see you next year! Please, register your interest to be sent the latest updates.
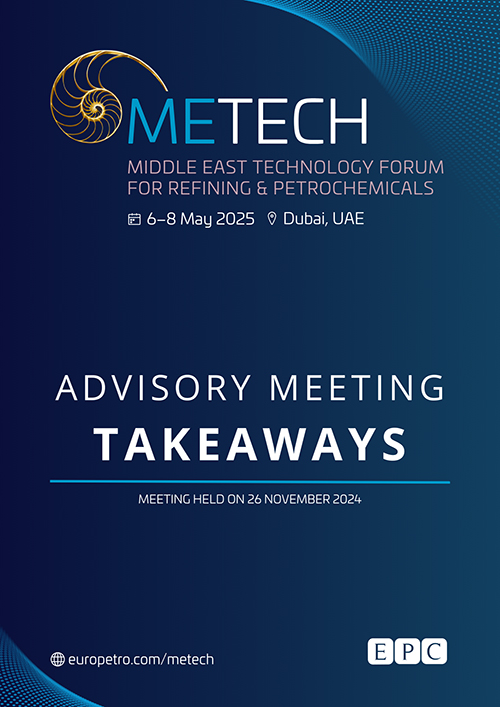
2025 Advisory Meeting Takeaways
Meeting held on the 26th November 2024
Highlights and key takeaways from the 90 minute discussion.
Download NowVideo Testimonials & Interviews
Contact the Organisers
For technology and equipment supplier, engineering company, professional services enquiries: kimberley@europetro-me.com
For refiner, petrochemical producer, chemical manufacturer, oil & gas operator enquiries: mark@europetro-me.com