In the downstream industry, commercially viable projects are getting more complex, requiring proportionally bigger resources and manpower, in order to secure completion on time and most importantly – on budget.
Critical infrastructure projects represent large investments and require significant resources.
As a result one important question springs to mind – who has such resources and time, and is available and ready to handle such intensive downstream projects? The question is simple and its answer can come from a special type of company - the EPC contractor, where EPC stands for Engineering, Procurement and Construction. This is a form of contracting arrangement used in our industry where the EPC contractor is made responsible for the complete range of the project activities, like from A to Z.
Securing project an engineering partner (and services), eases the pressure on the operator (client), since the EPC contractor has everything required, such as employed, and skilled personnel like engineers, specialists, craftsmen, admin and many more. By leveraging their resources, industry knowledge and experience, they are able to provide better service for the downstream clients.
It is important to highlight, that the operators remain in control during all project phases and have the final say when making critical decisions as well as when specific guiding is needed.
Another benefit to mention is that, by selecting a contractor, the operator does not sacrifice its current production operations, since instead of hiring a number of smaller providers, each needing its own bidding and contracting, the EPC contractor is a single business relationship and a single point of responsibility to manage. The main contractor can contract by itself subcontractors and vendors. However, this will fall under its responsibilities and will manage the connection between the client and subcontractors, by presenting on a regular basis the project status. For that reason, many operators choose to engage an EPC contractor when planning to initiate a capital-intensive refinery project.
Companies on the market differs from each other, but in an ideal scenario, the contractor provides a portfolio of bundle services including (but not limited to) concept design and development, feasibility studies, front-end engineering and design (FEED), execution of the engineering, procurement and construction and the final aim of both sides - commissioning and start of the production operations. The contractor provides turnkey project solutions and to partner with the operators throughout all of the project stages, ensuring the set goals are met and that the client will be satisfied with the result.
Concept Design & Development
With the project objectives and priorities clearly defined for your new facility, the EPC contractor can initiate work on the conceptual design. Based on operator requirements & specifications, the contractor will start designing the new units and all the auxiliary equipment and machinery needed onsite.
An operator can also envisage to retrofit existing assets which are still in good condition, but not profitable enough due to different market disruptions. To find out if this is possible, a skilled analytical team will have to make the required calculations, based on existing capacities, design limits, feedstock input, product output, catalyst throughput and other specifications needed for the existing static and rotating equipment.
Feasibility Study
It is compulsory to have at least one concept finalised and identified. However, it is always better to have a second (or benchmark) option - this helps the EPC project team to conduct the feasibility study, resulting in better estimation and narrowing of the project scope. During this stage, the budget and design estimations are both clearer, so the operator can determine which option will be better fit for the overall refinery scheme.
Front-End Engineering & Design (FEED)
Once the feasibility study has been completed, the EPC contractor can initiate the next step and move forward with the FEED, where the detailed design, engineering and procurement can begin.
At this stage, technical documentation will be created by the contractor team, such as diagrams covering the process flow, instrumentation, hazard analysis, health and safety protocols & etc. This documentation (created and maintained during FEED), will form the basis for the project; during the construction phase, and also will play an important role when the operator starts its production operations. During FEED, cost estimations are getting closer to the real numbers, allowing the involved parties to take further financial decisions.
Engineering, Procurement & Construction
Once all details have been agreed on both sides, construction work can begin. One of the main responsibilities of your contractor will be to manage staff labor, equipment and raw materials needs. The previous pre-project planning documentation will be used to guide the construction works. Another key responsibility of the contractor is its project manager and team to proactively troubleshoot any potential and foreseen issues onsite, as well as to maintain proper real-time quality assurance of the craftsmanship i.e. welding and construction inspections. Last but not least, the contractor is responsible to deliver the project in the expected timeline and budget of the particular scope.
Start-up & Production Operations
Commissioning of a production facility, brand new or retrofitted, is a labor-intensive process and it is advisable the contractor to stay onsite and to help the operator to initiate the production process. Once everything is up and running smoothly, the EPC contractor can handover the “keys” and all responsibilities to the operator – this step marks the project as ‘successfully completed’.
In some instances projects can be enormous in size, budget and complexity – so much so that it is impossible to have a single source EPC contractor – what are the options when this is the case?
Industry collaboration is the short answer: in the form of new legal entities JV (joint-ventures), combining resources for the common goal to be able to handle and execute such large-scale projects.
An example comes from SOCAR Turkey and its STAR Refinery located in Aliaga, Izmir Province, Turkey. The facility has already been into production operations for a few years. TSGI, a joint-venture consortium between four exemplary companies; Tecnicas Reunidas, Saipem, GS and Itochu, was established and was able to perform and manage the EPC phase of the 214 000 barrels per day grassroot refinery project.
The refinery installation includes a crude distillation column (CDU), vacuum distillation unit (VDU), naphta, kerosene and diesel hydrotreaters, hydrocracker, delayed coker unit (DCU), two sulphur recovery units and tail gas treatment, as well as featuring Hydrogen generation unit from processing liquid petroleum gases (LPG) and Merox treatment unit.
This project involved other companies such as the legacy FW Foster Wheeler (now WOOD Plc) and Fluor for the pre-EPC phase, Honeywell as a main automation supplier, FW USA designed the delayed coker unit, Technip Benelux provided hydrogen generation unit, while Tecnimont supplied the sulfur recovery and tail-gas treatment units.
In order to ensure trouble-free power supply during and after the project completion, ABB was responsible for providing the transmission and distribution substation, as well as the additional electrical infrastructure required onsite. Some of the other companies involved as sub-contractors in this project were Tekfen, Temelsu, Keller Grundbau and Samm Technology.
As one of the biggest investments in Turkey’s energy history, the development of the STAR refinery project has been estimated to have reached in excess of $6bn and involved 23 local and international banks. The facility has an advantageous location - being built on a peninsula with direct access to the Aegean Sea - the ability and comfort of using sea transportation for heavy equipment transportation, as well as to ease the import-export operations.
Another example involving international companies comes from Eastern Europe.
INA’s Rijeka refinery, owned by MOL Group, recently completed the biggest turnaround ever done within the facility and continues to run new conventional and alternative projects in parallel, such as a classic delayed coking complex and retrofitting its smaller Sisak facility into a bio-ethanol production and storage facility.
As main EPC contractor for the new DCU complex KT – Kinetics Technology, has to overcome a mix of complexity and engineering challenges, ranging from debottlenecking of existing production units up to the grassroot implementation of new ones. It involved implementing the latest solutions for coke handling and storage systems while the project involves over 60% of the existing refinery.
The Rijeka refinery is located on the Adriatic Sea shore and benefits from the direct sea transport for its new heavy equipment and logistics operations. However, the refinery by itself has very challenging layout - the facility is built on the side of the cliff and on multiple terraces. This means elevation differences with the new units, which many are located on different terraces and levels.
Such landscape challenges mean added challenges on the project.
However, INA’s management recently announced that the DCU project has reached an important milestone in early March. Key pieces of equipment for the complex were delivered to Rijeka, coming from Spain’s Tecnicas Reunidas and shipped by Spliethoff’s vessel – two coke drums each weighing 330t and having capacity of 900m3, as well as a 51 meters long fractionator.
These coke drums are an essential part of the technological process of the future complex and are just part of the numerous activities that are currently being carried out as part of the biggest turnaround program of INA’s history.
These examples highlight, that despite all the present engineering, transportation and global challenges, heavy and complex downstream projects are still moving forward in the various geographic locations.
It also clearly demonstrates that it is critical to select the right partner in the form of an EPC contractor with the right expertise and resources for your refinery projects.
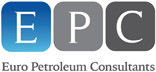
Published by:
