Today, digital technologies are present, available and an essential part of our work and our personal lives.
Like all innovations, when first introduced they have faced criticism and comparison with traditional methods. But in time the practical innovations always manage to prove their performance and efficiency.
Currently digital technologies and tools are in a similar situation. The recent Covid19 pandemic, with all of its negative impact, has been an unprecedented reminder of how much we rely on technology and how important it to be properly implemented within the working and production processes.
Without doubt, the biggest asset any refiner or petrochemical producer has is its workforce. This is the first sector that can benefit greatly from the available digital communications technologies and support ensuring the effectiveness of the people onsite.
The Refining business relies on good communication between all involved parties – this is to maintain a profitable and healthy process, as well as keeping high safety levels.
Here is the first example of implementation, even during the worst period of the pandemic people stayed in touch, even remotely. The business and production units within the companies were provided with ready available solutions, which allowed them to stay connected and maintain their businesses in the extraordinary circumstances.
One of the common tools implemented with immediate effect, around the globe, was the Microsoft Teams solution. This solution benefited from its implementation within the company’s office tools applications portfolio, including the company email and schedule calendar. Such multi-device solutions have proven their efficiency, enabling a quick reaction when needed. For example, a scenario where a young process engineer needs advice and a quick reponse from a senior process engineer within a production facility.
The solutions are mobile-friendly too, so this is a great digital communication benefit, allowing people to stay connected in real-time. These mobile solutions, often categorized as wearable devices, can also support an augmented-reality features. The idea behind the mobile solutions is that they are able to connect and interact with the main control room systems and operators, allowing data exchange, as well as detection and mitigation of critical risks such as accidents or leakages.
An example is coming from the software used by technicians in the field. Digital solutions can help to check the status of equipment, visualize standard operating procedures and work instructions, allowing to communicate the completion of tasks in real time and to immediately trigger the next interventions in the field.
Digitizing All Aspects of the Refining Process
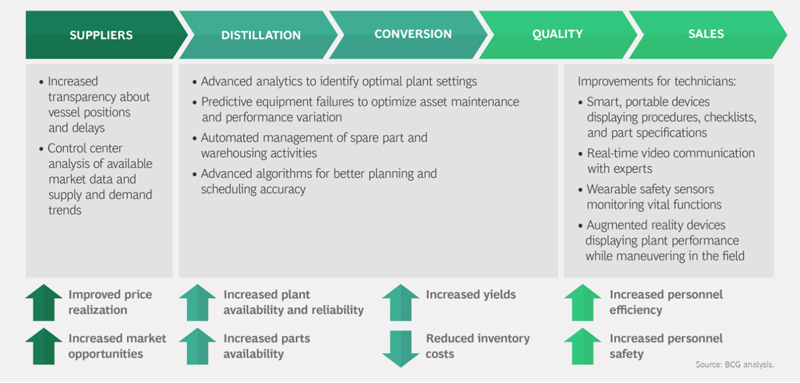
Source: BCG Digital Refinery Analysis
Let us say that the remote communication is set, people are aware of what they need to do, know who to ask for advice if needed, also know where and how to check for information. Next segment for digitalization is the production analytics and this is where the true digitalization journey begins.
Refineries are complex facilities and cannot rely on simple automation and non-connected data management solutions any more, since the current production excellence requirements for precise operations are getting more stringent. Process control is getting more advanced, so refiners must identify with what scenarios they might have to deal in their daily operations. Once those parameters are set, the so-called reality health check unlocks the next steps where the automation and digitalization strategy can be re/designed and further implemented in a convenient and accessible way for the refinery employees.
Apart from the final refinery products such as liquid fuels and base chemical blocks, refineries also produce an enormous amount of production data, gathered by the refinery sensors and metering systems. Here is the question, where and how this data is stored, also is it stored in a convenient way for extracting valuable information to support the variety of important decision makings.
In an ideal scenario, that data has to help on improving the production yields and can be split in two important parts. First, advancing the production analytics with real-time characterization of the production assets, including feedstock input and product outputs, which allows to define the optimal plant regime. Second is the supply chain optimisation, where the machine learning (or the modern term AI) can support to precisely predict the exact product portfolio that is or will be available, overall leading to improved scheduling accuracy and campaign planning for optimum margins.
Successfully implemented web-based tools are an example for optimized production planning, where the most wanted feature is the tool to be able to predict crude slates compatibility. Main task for these tools is to extract valuable data from blended crudes and to predict further potential processing issues.
Another important question is if digital means safe and secure? One or two decades ago, security bridges were present, which is one of the main reasons why people can still think that digital is not safe enough to be implemented in strategic facilities such as refineries. However, communication and information technology have evolved and nowadays digital security is brought to another level. When we talk about sensitive data, the latest trend in data exchange is the end-to-end encryption method set on the physical devices and over the communication infrastructure, which is cloud based.
This means that even if the refinery data somehow leaked or devices are physically stolen, the data intruders won’t be able to read or do much with this data, since the encryption levels are now far more advanced than the analogue example from the 20th century, the Enigma machine.
Last but not least, the digital predictive maintenance tools are a must have technology to be implemented in modern refineries systems. There is not a single maintenance engineer, who doesn’t want to work with advanced asset reliability maintenance systems, since as we mentioned, manual processing and analysing of the data is getting close to impossible in order to comply with the modern ways of working. So, refiners are now able to improve their asset reliability through advanced maintenance management, using big data and machine-learning algorithms to optimize maintenance cycles and predict critical equipment failures.
Such developed big-data algorithms are set to extract valuable data, give refinery staff the flexibility to predict one of the most common issues within process - the evaluation of the critical equipment fouling levels. Adapting these techniques helps engineers to identify the important factors that can lead to future problems, allowing the refinery staff to avoid unplanned maintenance events and production downtimes.
These examples highlight how digital innovations can be used within the downstream industry to help producers achieve their objectives – to operate their assets safely, efficiently and profitably.
Written by:
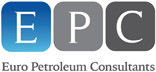
Published by:
