The Industrial Internet of Things (IIoT) and it associated functional agility and data management improvements will catalyze significant improvements in the Process Industries. But, it will be resisted by many.
What is IIoT that it is so threatening? The author prefers this definition:
"Industrial Internet of Things: A system comprising networked smart objects, cyber-physical assets, associated generic information technologies and optional cloud or edge computing platforms, which enable real-time, intelligent, and autonomous access, collec-tion, analysis, communications, and exchange of process, product and/or service information, within the industrial environment, so as to optimise overall production value. This value may include; improving product or service delivery, boosting productivity, reducing labour costs, reducing energy consumption, and reducing the build-to-order cycle." (‘The industrial internet of things (IIoT): An analysis framework' Authors: Hugh Boyes, Bil Hallaq, Joe Cunningham, Tim Watson)
Translation: An Ecosystem of Agile Functionality, including configuration and data management, with Transparent, Verifiable Actionable Data visible to all. In other words, IIoT is another example of the vendor-neutral Componentization of MES and Control Systems. There are two prominent efforts to componentize those systems:
- Industry 4.0 in Germany. This is a very broad effort that publishes its work for all to use. One can easily work with a demo system.
- The Open Process Automation™ Forum. It appears to be focused on reliable input to cloud-based servers to do basic control. It does recognize that control can be performed in the “Edge Device”, aka, the local sensor’s or actuator’s controller. As such, its current scope appears to be much narrower than that of Industry 4.0.
If you view IIoT as networked devices, then both of these efforts do that. The main difference between these efforts and IoT is that IoT uses of more generalized communications methods and data communication structures. IIoT will derive from IoT. This IIoT difference brings more creativity and ingenuity to the table. That competition will benefit the process industries – after the disruption settles.
IoT devices are designed to operate in a variety of ecosystems, including 5G. (IoT devices are purportedly 5G enabled. They just need the 5G infrastructure.) As such, fields, like healthcare, home monitoring, etc., will evolve ways to manage and gain real-time, actionable knowledge from millions more sensors. Ecosystem providers, like Apple, Amazon, Google, will lead the way on innovative approaches to help us live longer and healthier lives. Some of these healthcare concepts will be applied to personnel working in hazardous environments.
As these IoT tools and techniques are brought to Industrial Devices, IIoT will develop quickly. IIoT will provide the impetus for methods to manage and use distributed components manufactured by a variety of vendors in an efficient ecosystem.
The Benefits of moving to a componentized, open, agile, transparent ecosystem are well documented.
Many historical automation suppliers are now delivering solutions in parallel with their historical offerings.
FieldComm Group (FCG) is leading a way to retrieve configurations from existing devices – independent of their communication protocol and system connectivity. This data collection capability coupled with sophisticated site-wide configuration management will facilitate the move to IIoT devices. Such verifications can also be combined with cybersecurity techniques to ensure security at the same time as ensuring that there are no other unauthorized changes.
In many respects, FCG’s efforts will enable most traditional devices to be treated like IIoT Devices. This will expedite the move to IIoT. But, it will be resisted, because it may expose the inconsistencies in thought versus deed. Remember Macondo Deepwater Horizon was preventable! Had the real capabilities and state of the equipment had been exposed to the general organization, Management would have had no choice but to mitigate the situation. IIoT facilitates broad exposure of the real state of capabilities versus the rosy picture depicted in the HAZOP that sits on the shelf – totally unused! IIoT has the capability to convert the HAZOP to Actionable Data that can be periodically, programmatically compared to the current equipment capabilities and configurations. Such periodic verification will mitigate another Macondo. When such verification is automatically performed and reported as a public record, trust in the Process Industries will increase.
IIoT will not evolve without its challenges. For instance, ecosystem management, configuration management, security, and notification flooding.
- By definition, every site is its own ecosystem. That is, the site has its policies, procedures, regulations, etc. that define the required capabilities of systems, components, subecosystem, etc. to interoperate within their site. To provide a high return, all components must interoperate with as little effort as feasible (Plug’n Play as mentioned above is the goal). IIoT requires formalization and active management of those ecosystem rules.
- Since these devices can be configured for multiple services, businesses will need to move to periodic, proactive verification that the configuration is as approved.
Fortunately, New techniques, like those for configuration management by FCG and Industry 4.0, are being developed to define security zones and to identify unapproved changes to devices. - Since IIoT devices can send Notifications in conjunction with or independent of a Control System, a single site-wide notification management system needs to evolve, or sites will experience “Alert Flooding”, like Process units experienced “Alarm Flooding” for decades.
This enhanced site-wide configuration management will expedite the move to each site creating their own Virtual Development Operations (DevOps) Ecosystem for MES and Control Systems. By definition, DevOps is an Agile Digital Twin. DevOps is cloud-based and will cause significant redeployment of personnel and elimination of some in-house data centers. This will enable significant IT Budget to be Allocated to IIoT type projects and enhancements.
Path Forward: Talk with your existing and possible automation vendors to learn the “Art of the Possible” – changes that can be made in a relatively short time frame without disrupting your existing systems. In PERA.net terminology, these are called “Opportunities” for improvement. Understand their Cost and Implementation timeframe with the Associated Benefits, ramp up, and duration. Then, do your own www.pera.net style Master Plan to select Opportunities that meet your Investment Criteria and prioritize those “Opportunities” into Projects to develop a Transition Plan.
IIoT will be the catalyst to evolve DevOps sooner rather than later. Yes, IIoT is a component of Digital Disruption. As documented elsewhere, management must lead the way to breakdown the historical silos. Each process industries company needs its Satya Nadella.
Yes, the potential benefits are so significant and the challenges so strong that the CEO or at least Senior Management must LEAD.
Learn more by attending OPEX MENA 2020 – Excellence in Safety & Operations, 31 March - 2 April 2020 in Bahrain. Visit www.opex.biz for more details.
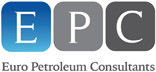
Published by:
