Plastics have been inarguably a serious issue for many countries of the world, contaminating oceans and land: recent researches of environmental agencies found out that microplastic elements were to be found in fish bodies, etc., being then consumed by people, and even possibly nanoparticles could reach human lungs via air. The problem is yet to be solved in two ways: preventing further spreading of plastic waste and collection of existing amounts of it. With this article, we will address the issue of sustainable plastics production and recycling.
Demand for petrochemicals has increased by more than 50% over the past 10 years and we expect the sector to remain a large user of oil in the next few decades. Currently using about 10.6 million barrels per day, we expect the industry to require between 14.9 mb/d and 23.4 mb/d by 2050. Barclays bank research expects petrochemical consumption from oil-based products to constitute 20% of global oil demand by 2050, up from around 10% today.
The majority of recycled single-use plastics degrades in quality, which means that water bottles cannot be recycled into more water bottles, and instead are converted into textiles or carpets that are non-recyclable. a complete ban on single-use plastics would lead to a demand reduction of 5% relative to our base-case forecast. Our dynamism case assumes 75% recycling, but not a complete global ban on single-use plastics.
We have been discussing reasons for increasing petrochemical demand, and the most obvious ones are urbanization and new applications/product variations. The trend under consideration – recycling – will be pressing down the prime resin and polymers design, therefore IHS market predicts global petchemical demand growth to reach 350+ mln. tpa (previous forecasts were more positive). 2019 and 2020 featured a global manufacturing downturn, major supply disruptions in chemicals and energy, government policy changes, and 2021 promises to be challenging. Most of the major planned projects in the industry were not canceled, and shall come online this year and in 2022, bringing uncertainties to product prices due to certain overcapacity in PE, for instance. The circular economy has already a certain impact on polymer production, and yet we see a lack of recycled PE.
Global Plastic Product and Packaging Manufacturing industry grew to an estimated worth of 560 billion USD in 2020. Properties that plastics provide in consumer products are cheap, lightweight, durable, and resistant to chemicals, act as thermal and electrical insulators, and can be easily processed into a wide variety of products. CAGRs of global plastics recycling market are predicted to be 5 7% for the years 2018 through to 2026 market by 2025, to be worth 67 bln. USD.
Key drivers globally are the availability of advanced technology, the skilled Workforce, and the Large-scale residential and industrial facilities (infrastructure). Four major plastic resin types, namely PET, HDPE, PP, and LDPE, dominate the global recycled plastics market. The largest of these segments is PET, with a 2017 market share of 55%. Increased demand for recycled PET products is likely to emerge from developing countries, including China and India. Surprising as it may seem, but India is the leader in terms of plastic recycling - a 60% rate – the least amount of plastics was recycled in the US (9%), so regions like GCC, China have a road ahead them to follow the trend.
Europe and the US are major exporters of waste plastic for recycling that directly depend on China. EMEA contributes to 35% of the global market. APAC region provides more dynamic prospects because of increasing consumer-driven economies and industrialisation. Innovation is one of the few sources of competitive advantage. A larger proportion of globally traded used plastics are being recycled in India. This is attributable to the availability of labor, low installation cost of recycling plants, and cheaper freight and logistics, and legislation. Used bottles will likely remain the leading source material for recycling.
The EU had set out a target that from 2025, PET bottles will have to contain at least 25% recycled plastic. ICIS expects global soft drink producers to meet or exceed this (R-PET) target.
Increased focus on sustainability will additionally affect PP demand and trade in the region, as countries in the region ramp up efforts to go environment-friendly.
While plastics are part of almost every solid waste category, the largest share was in the containers and packaging – 16+ million tons in 2019, incl. bags and wraps, PET and HDPE bottles, containers, and some other nondurable items. However, we shall not forget the wide use of plastics in the manufacturing of furniture, appliances, and so on. Altogether they contribute to a significant part of routine life in developed countries, and it was not until the mid-2000s that plastics waste management became ‘a real thing’, but recycled plastics still have not reached 15% of the overall waste amount, another 20% undergoes combustion with energy recovery, but the rest is landfilled. The most important activity in the direction of waste management was raising the consciousness of consumers, but production and R&D possess a strong potential to change the unfavorable ‘balance’ towards better disposal.
Several approaches are available to address the environmental side effects of ever-growing plastics production, use, and disposal:
- Changes in product design, incl. use of alternative sources – i.e., bioplastics that we reviewed a year ago, or design practices (similar to car manufacturing when car bodies were made not only of metal, but also of carbon fiber)
- Efficient collection and recycling processes, the most important being clean up and remediation activities.
- Using products more intensively like reinforced composites (e.g. for wind turbine blades), Reducing losses along supply chains, and Increasing product lifetimes
Use of alternatives to plastics or biodegradable ones still impose a threat to environmental stability due to associated technology risks, thus the displacement of virgin plastics by their recycled equivalents makes plastics recycling viable and desirable in the mid-term. Recycled plastics production even 10 years ago used to be tenfold less energy-intensive than virgin one (over 80 MJ per kg), and since then the process has improved.
Generally, there are two main categories of plastics: thermoplastics and thermosets. Thermoplastics constitute familiar plastic objects; thermosets are more specific in use. Whereas thermosets cannot be effectively recycled, most thermoplastics can.
In IEA’s CTS (Clean Technology Scenario IEA) plastic recycling increases sharply by 2050 tripling since 2020, resulting in a 7% reduction in primary chemical demand. On the other hand, in the CTS, the global average collection rate of plastic waste increases nearly 3 times by 2050, leading to increased production of recycled plastics and a cumulative saving of around 5% in high-value chemical demand, compared to current trends. This scenario assumes that plastics recycling contributes to 9% CO2 emissions reduction, savings in recycling and switching to coal-to-gas feedstock can be as high as 200 billion USD. The UK is planning to tax companies that don’t use at least 30% recycled plastic in their products, but until then it may be cheaper for companies to demand more new plastic to make their packaging.
Today there are two main ways of plastic recycling: mechanical and chemical recycling
- Mechanical, or “back to polymer”, recycling offers a simpler and generally lower cost source of secondary plastic production, in which the chemical structure of the polymers remains intact. Collected and sorted plastic waste is the feed material, which is then cleaned, cut up into chips, and re-melted ready for molding.
- Chemical, or “back to monomer”, recycling describes a group of processes in which the plastic waste is converted back to the chemical building blocks that produced the original virgin material. This involves chemical transformations, calling for complex industrial processing equipment, and thus is generally more capital-intensive than is mechanical recycling. The key advantage of chemical recycling is that the quality obtained in secondary plastic production is often equal to that of virgin production, enabling the same product to be recycled many times. The difficulty, though, is that the process economics tend to be less favorable relative to the virgin production routes for the same plastic.
Recycled polymers are expected to gain an increasing foothold, especially in more developed economies, as global brands embrace sustainability under growing pressure from consumers, the media, and environmental policy. Even though unfavorable economics in the recycled plastics markets are expected to continue in the first half of 2020, but media and consumer pressure should boost demand globally. S&P Global Platts estimate recycled plastic to cost an extra 72 USD per tonne compared with virgin plastic. Forecasts say global recycled plastics volumes reached nearly 20 million mt in 2020, or 8% of total virgin demand.
Umicore N.V. – a European chemical company - reached revenue in 2019 of 15 billion USD - the company is focused on catalysis, energy, and recycling. Umicore generates most of its revenues from clean technologies such as emission control catalysts, materials for rechargeable batteries and photovoltaic cells, fuel cells, and recycling.
We see some recent positive developments: last December General Electric signed a contract for recycling of wind turbine blades into cement production composites, which can lead to further decrease of carbon intensity of the process by 27% - this is a good example of synergy effect of different technologies to decrease environmental impact. In addition, a partnership is highly beneficial in innovations that help mitigate industrialization drawbacks while generating margins in the future: SABIC collaborated with Plastic Energy to build in just 2 years circular polymer production plant. Coca-Cola’s European business plans to cut the amount of virgin plastic used in its soft drink bottles to 50% within the next two years and will change the color of its Sprite bottles from green to clear to make sure 100% of its bottles can be reused. In Russia, the country’s largest petchemical producer – SIBUR – supports transition in Russia to the principles of the circular economy by changing feedstock model, eco-efficient production processes, product safety, and better quality, promotion of recycling by favorable regulatory environment.
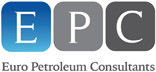
Published by:
