One key industry question currently being asked is whether Energy Efficiency of processing facilities are part of future sustainability plans and solutions? The answer is a definite and resounding yes.
Improving the overall energy efficiency means reducing the overall carbon emissions of the facility, which should be seen as the 1st major step on the Sustainability journey.
Investing in such technologies and upgrades does not come cheaply. However, with the introduction Carbon taxes, good planning and efficient budgeting such investments can pay off on their own.
It can be seen that the level of energy demand increases in complexity and can have low and high energy efficiency levels.
The difference between energy efficient refineries and those that are less efficient represents a real opportunity to rationalise energy consumption.
Inefficient refineries can reduce their own energy consumption by as much as 30% through more efficient technological, energy and organisational solutions.
This can be illustrated as follows: a refinery, which accounts for 5% of the energy consumption of crude oil, has to work 16 days a year to meet its own energy requirements.
Energy savings go right to the bottom line. Money that is not spent on energy is money that can be kept and put to other uses. Energy reductions lower operating costs and can reduce maintenance costs also. On the other hand, poor energy performance steals capital that could be spent on other business needs.
Energy reductions promote emissions reductions. Emission reductions promote reduced compliance requirements. Reduced compliance requirements promote reduced fees, penalties and reporting; and reduce the amount spent on chemicals, environmental controls, etc. The current scenario sees:
- World Population growth 15%
since 2010
- CO2 emissions 40%
since 2010
- Competition is more severe than ever
Financing, rebates and tax incentives are now readily available for plant & asset improvements.
As energy efficiency improves, costs are further reduced, and the company as a result more competitive.
Price fluctuations can be a significant risk factor that can be reduced by implementing an energy management system to reduce energy consumption.
Refinery performance indicators and relationship to resource efficiency (example):
- Production optimisation (+40% efficiency)
- Feedstock and energy consumption (- 30-50%)
- Environmental protection and safety (up to 50% OPEX of the refinery)
- Maintenance (repair time -25%)
- Equipment utilisation/loading efficiency (+40%)
- Efficiency of organisation (+80%)
- Resource efficiency: EBITDA/bbl +2-3$ => 150-200 mln USD/year (10 mln t capacity)

SOURCE: Paul W. Griffin, P. Hammond and Jonathan B. - Industrial energy use and carbon emissions reduction: a UK Perspective. WIREs Energy Environ 2016
Energy efficiency in production always consists of three (3) key steps.
1 The first is to address the 'low-hanging fruit', i.e. replacing light bulbs with energy-saving ones, putting in frequency and speed controllers for drives and so on.
Example of a company - strategic energy saving goals include:
- Modernisation of technological equipment & introduction of energy-saving technologies;
- A highly efficient system for managing electricity consumption;
- Optimisation of generation & consumption of thermal energy;
- Development of own generation sources.
This particular company also achieved more rational use of fuel and energy resources and as a result made substantial savings (>USD 100 million) through the introduction of innovations that reduced energy consumption.
2 The second step is to optimise equipment that uses a lot of energy, such as compressors, pumps and air coolers. Optimisation comes down to two things - moving to condition-based maintenance and monitoring the condition of the asset in real time to make sure the equipment is running well. The second is finding the most energy-efficient operation modes for the equipment and using them specifically.
For pumps, we find the point of maximum efficiency based on performance, energy efficiency and equipment exhaustion.The task of finding the optimum point for a compressor is more complicated, usually involving a survey and a model of the equipment, from which the optimum mode is calculated.
Refinery power engineers are usually familiar with the first two steps, and the third step is a complete process energy monitoring system.
3 In Europe and the USA, these systems are an integral part of any production plant, and practically every plant has an energy manager reporting to the general director, whose ‘sole’ task is energy efficiency, as opposed to our plants' chief power engineers, who have the main KPI of uninterrupted power supply.
The task of this system is very simple - to create energy metrics for all types of equipment, processes, products to create current energy consumption standards for all of the above and monitor energy consumption to comply with these consumption standards.
Initial step is to retrofit the necessary metering devices and to collect information on the energy consumption of all equipment, storing it in a ‘data lake’.
The second step is to implement an energy management system that works on the basis of contextualised information from technological processes. All production processes are decomposed into a hierarchical structure that contains all equipment, and based on this the actual consumption rates for each piece of equipment are calculated, and deviations from these rates are analysed, and the system issues alerts and supports solutions to eliminate any deviations.
The importance of accurate material and heat balances, for this system to work properly, cannot be overstated - you cannot manage what you cannot measure. By reconciling the balances directly, we will inevitably get errors related to the accuracy of the instrumentation, faulty instruments, losses and sampling. Simulation on a mathematical model calculates how unbalanced the flows are.
In terms of numbers, energy savings from the waste heat recovery process are the most significant, with energy consumption 92.37% lower than for the normal rectification process and 52.50% lower than for the heat pump rectification process. The waste heat recovery process has the lowest economic costs, 87.06% lower than the normal rectification process and 44.78% lower than the heat pump rectification process.
Deeper refining is one of the ways companies can save resources by getting 1.5 times more petroleum products out of 1 tonne of oil. As the refining industry is among the most capital-, material- and energy-intensive industries, it is clearly important to optimise refinery operations and get the most out of current assets.
Possible ways to optimise raw material consumption:
- Increasing conversion rate per tonne of raw material processed
- Increasing productivity of process units (higher yields of key products)
- Minimisation & loss control of raw materials and products
- Reducing fuel and energy consumption
- Optimisation of process configuration
Energy consumption is one of the major cost items in any refinery. In order to maximise the benefits of improving company-wide efficiency, a significant number of small and medium-scale plant-specific programmes usually need to be implemented. With relatively little investment a downstream refiner can potentially save tens of millions of dollars per year by reducing energy overhead by 50-70% and be on par with its competitors in the upper quartile. We would also add a point regarding environmental protection. In this case, for companies, this factor becomes more and more significant every year in terms of costs, product quality, production safety, and the overall reputation of the company. For example, for a large company this cost item is becoming increasingly significant due to increasing adverse environmental impact and is comparable to capital expenditures in the refining sector or 50% of the refining operating costs, so improving environmental policy together with resource and energy conservation can have a significant positive effect on financial health.
The efficiency improvement programs offer the following benefits to certain refineries - case:
- Efficiency improvements of up to 30-40% with little or no capital expenditure: priority activities (Quick-wins) - 5-10% reduction; no/minimum investment - 25-30% reduction;
- Quick-hit interventions generate revenues quickly without capital investment within 3-4 months;
- Improvements with no/minimum capital investment yield significant benefits within 6-12 months;
- Improvements are based on implementation of best practices, resulting in sustained savings year after year;
- In value terms, the benefits are valued at tens of millions of dollars per year – which is highly significant.
- Starting from the main refinery heat source the tube furnaces/fired heaters, which we know are very sensitive installations in terms of efficiency tuning. There is room for improvement in each fired heater in order to get the maximum efficiency from the radiant and convection sections inside. It is not so straightforward like if you need more heat, just to increase the fuel supply to the burners and then the problem to be solved. Sometimes, it could be a temporary solution, but in terms of environmental effect and energy cost it is not reliable in long-term, also it is strictly independent case in each facility.
As we can see Energy Efficiency of processing facilities will play an important part of any future sustainability plans and solutions. The simple fact remains that improving the overall energy efficiency means reducing the overall carbon emissions of the facility.
And this should be seen as the 1st major step to sustainability.
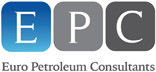
ESF MENA - Energy & Sustainability Forum for the Middle East region is taking place from 24th – 26th October 2021 in UAE. For more information, please visit esfmena.europetro.com
Published by:
