The development of the global oil & gas chemical industry is cyclical and in recent years has been characterised by consolidation of production capacities, a shift of large-capacity oil and gas chemical facilities to regions with cheaper feedstocks, convenient logistics and/or dynamically growing demand, and an active role of the state in the development of new oil and gas chemical centers.
The key factors of competitiveness remain low prices for oil and gas processing feedstock, the cost of finished product logistics, and not forgetting low specific capital costs when constructing new facilities and expanding existing ones.
When looking to adopt long-term strategies, major industry players consider a number of factors & parameters – these include events that may have a serious impact on the value creation process in O&G complexes, including:
- Reduction of investment attractiveness of North America and ethane export from the USA
- Increased trade tension and sanctions
- Long-term trends in plastics recycling and reuse
- Lower than expected growth demand in China
In a relatively short period, O&G chemical complexes have gained strong positions virtually on all continents, accounting for 5 - 10% share in the economy of many countries. O&G chemistry is a connecting link between many of the major industries; from oil and gas complexes and processing industries, through mechanical engineering, to aerospace, and telecommunications – and the list is long.
When looking at the revenue of Exxon Mobil, BP, Royal Dutch Shell, Total, Chevron-Texaco, Conoco Philips and others, chemistry accounts for more than 10%. In general, at least half of all O&G-chemistry products are produced by oil and gas companies.
If we take a look at the Black Swans Disrupted trends of 2019 – Resulting in Unbalanced Market Demand & Supply Growth
- Global capacity could grow by ~40 to 50% to over 2 bln. tpa by 2027
- Over 1,300 planned and announced plants to come online primarily in Asia and the Middle East
- 2020 - > 4 mln. t additional volumes in China alone (mostly LLDPE/HDPE
- Demand increasing in Asia and ME, but there is a cap for growth
- Global Capacity growing, European producers losing their market positions
- Process Efficiency improving
- Demand for environmentally-friendly products with high added value
- Opportunities for supplying local markets with specialty products
- Investment in R&D will help with strategic goals
In regions like the Middle East or Russia, there are increased signs of consolidation and integration, mergers and acquisitions, the market for oil and gas chemicals is becoming oligopolistic. In Russia, for the successful development of the oil and gas chemical industry, it is necessary to solve one of the key structural problems - to eliminate the shortage of capacity for the production of monomers (primarily pyrolysis). On the one hand, Russia has an excess of oil and gas chemical raw materials, which will continue to grow until 2030. On the other hand, there is a potential for a significant increase in demand for O&G chemical products, the raw material for which is the production of pyrolysis. It is believed that Russia has good prospects for an important production of plastics, rubbers, organic synthesis products - both by increasing domestic consumption by reaching the world average level and import substitution, and by expanding the export potential to the key regions for Russia; namely Europe and China.
By the end of the forecast period demand will have increased by almost fourfold from existing levels, and the share of feedstock processing will increase to 55% of its output, against 28% in 2010.
In terms of turnover, global trade in polymers is approaching the volume of ferrous metallurgy products. The market value of certain low-tonnage products sometimes exceeds the price of gold and precious stones. After four or five stages of processing of hydrocarbon raw materials, the cost of final products increases by 8-10 times. For example, this is the chain: natural gas - ethane - ethylene - polyethylene - polyethylene products. Some products at the 7-8th stage of oil and associated petroleum gas (APG) processing exceed the cost of similar raw materials by 100 and more times.
For the global O&G chemistry, the main driving forces are innovation, new technologies and products. The modernised industry is based on so-called mega-installations, which provide good technical and economic indicators due to high technical equipment and "scale effect".
Looking at the Petrochemical sectors current structure with regards to the existing raw material base; the global average ratio is 60% crude oil and 40% gas. In Russia, the largest gas-producing country, the share of gas is 25%. Japan and the EU, i.e. traditional raw material importers, have approximately the same indicators. In the US, Canada and a number of other oil and gas producing countries the share of gas raw materials, ethane, propane-butane, etc. in the consumption of O&G chemistry reaches 70%.
According to certain calculations, the gas potential of valuable components for the gas chemical industry is at least 50 million tons. rational utilisation of APG. Preliminary calculations of efficiency of typical gas-chemical complexes with different specialisations: basic, propylene and propylene products production, "polymer "chemical" and "petrochemical", show the internal rate of profitability of projects from 16 to 25%. Net discounted income ranges from $31 million to $231 million.
The modern gas processing plant with an average capacity, processing of 3 billion cubic meters per year, costs at least $400-500 million with a payback period of 5-7 years and more.
It is expected to see certain changes in the structure of manufactured products: Chemical products with fundamentally new application possibilities will appear on the market. This will be associated with thermoplastic composite materials based on polymers; plastics with a long life cycle; materials capable of self-adaptation; high-tech fibres of the new generation; self-healing eco-rubber; "smart" nanomaterials, changing the shape at the request of the user; amorphous polymers, restoring damaged coatings; biocompatible and biodegradable materials, etc.
The overall industry development will directly depend on the coordination of activities throughout the chain: production - oil and gas processing, including APG utilisation, fertiliser production, as well as methane production from coal seams - NG chemistry, which should now be considered as a single industry, the final products of the chemical complex.
Looking Ahead: Opportunities for Green Innovation
Specialty chemicals may play an even larger role in sustainable development in the future, as opportunities for green innovation are substantial. Specialty chemicals are sold on the basis of performance or function, not chemical composition. Consequently, price is important but not imperative. In addition, specialty chemicals are closer to the consumer than commodity chemicals. Products that include "green" specialty chemicals can tap into consumer interest in the environment and bio-based ingredients.
Paths to greener specialty chemicals include the use of:
- Sustainably produced renewable feedstocks
In general, bio-based materials have smaller carbon footprints than their petrochemical counterparts. But there is a caveat: feedstock provenance matters. Land-use changes can have a major negative impact on carbon footprint. Specifically, the drainage and deforestation of peatland to make way for oil palm plantations increase the environmental burden of palm oil, palm kernel oil, and their methyl ester derivatives. Because of land-use change, these materials have large positive carbon footprints. In contrast, coconut oil and coconut methyl ester have negative carbon footprints - that is, their production removes carbon dioxide from the environment. - Biocatalysts & biotechnology
Biotechnology offers a sustainable route to value-added products. A case is stevia sweeteners. First-generation stevia sweeteners are extracted from the leaves of the stevia plant. The extracts contain many components but only traces of the best tasting sweeteners. Next-generation stevia sweeteners are produced from corn or sugarcane by yeast fermentation. - Waste materials as feedstocks
Using waste materials as feedstocks supports the circular economy by recycling "waste" into useful products. Examples of specialty chemicals that can be produced from waste materials include polyols from waste gas (such as flue gas from steel mills and off-gases from refineries); furfural from biomass (such as corn stover, corn cobs, and sugarcane bagasse); and polyhydroxyalkanoates - biodegradable polymers - from biogas (through anaerobic digestion). - Urea Demand
is growing as a consequence of 1) increasing food consumption and 2) strong demand of urea in technical applications (i.e. melamine and DEF). Global urea demand is currently 167 MT per year and expected to grow at 1.5% annually, up to 179 MT by 2022. Urea production cost drivers are natural gas feedstock, low plant construction cost and operating cost. Strong growth of urea demand in Russia and FSU due to increasing fertiliser practices and melamine demand. In addition to anticipated slow down in capacity expansion, upward price potential from 2019 onward.
Trends in Middle East that Affect Petrochemical Industry
Refining Capacity
Refining capacity is expected to increase from 10,646 mbd in 2018 to 15,558 mbd by 2023 accounting for over 76.6 per cent of the total refining capacity of the region in 2018.
Feedstock
The Middle East is the largest PP exporter in the world, with over 40% of its volumes coming into Asia. Natural feedstock cost advantage will continue to support Middle Eastern PP producers’ margin. Middle Eastern refineries are largely dependent on naphtha, a crude oil byproduct, for petrochemicals. The region used over 5 million barrels of oil as a petrochemical feedstock in 2019. It also produced a substantial amount of ethane from natural gas liquids, and ethane is expected to make up 45% of Middle East petrochemicals by 2021.
Demand
Middle East producers are expected to face intense competition from both US and Chinese producers. Demand for finished consumer goods within the region remains relatively flat. Processors who used to hold stocks for a month are today not keen to hold inventories for more than 15-20 days fearing future price reductions, which means purchase volumes are almost cut by half. Increased focus on sustainability will additionally impact PP demand and trade in the region. Global supply surplus is likely to extend its influence over PE prices.
Opportunities
- >+ 3% / year until 2027 - global demand growth for polyolefins
- Despite production increase, deficit of polyolefins may be expected in post-2021 period
- Coverage of this deficit is an opportunity for polymer producers worldwide
Constraints
- There is limited demand growth outside of Asia, and declining demand in North America
- Asian imports into GCC will still be expected, primarily from China, India and Taiwan, to help meet GCC demand
- Asia Plant utilisation rate is projected to fall to 66% in 2020 from 75% in 2019 leading the trend in other regions
To summarise, continuous innovation remains vitally important. As a result of innovation, chemical companies can obtain the following results:
- additional client-oriented or data-based models
- increased localisation of activities and reconfiguration of supply chains to get closer to customers
- a sharp reduction in output, which is compensated by the use of new monetisation models
- an increase in the number of partners and an expansion of the ecosystem of companies to distribute the risk of development, complement technical competencies and bridge the gap in the value chain with end users
- an increase in the use of technologies, in particular artificial intelligence
- transformational changes in the company's identity and culture to realise new opportunities
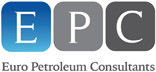
Published by:
