Catalytic processes are at the heart of all refineries and petrochemical complexes. The global catalyst market is booming, with continuous technology developments in catalyst production, optimization and increased efficiency in achieving operating goals. This trend is especially true in the refining sector where the use of catalytic processes is on the constant rise.
Global Trends
Key drivers for global catalyst demand growth:
- A wave of new downstream capacities addition, which in turn is generated by demand for fuels and petrochemicals (automotive park growth, higher quality of life, urbanization, etc.)
- Enhance efficiency of downstream processes: conversion level, target products yield to address market changes, energy optimization reliability and better use of all sources
- Stricter environment and safety regulations worldwide – both for fuel specifications and composition and for environmental impact
Markets: Supply & Demand
The Global Catalyst market is forecasted to grow at CAGR of 4.6% by 2024 – further expansion is expected with developments in refining, petrochemicals, chemicals and evolving environmental factors – all increasing demand for more performant catalysts, and investment in R&D. The demand in refining catalysts is forecasted to reach over $4.7 bln. this year (annual growth slightly lower than global sales of all catalysts – 3.6% per annum – signs of a potential misbalance in some regions, esp. on mature markets, in the upcoming few years).
FCC catalysts – which we will look at in greater detail – already represents the largest market in terms of value and will show the fastest growth. Catalyst demand for petrochemicals and polymers production will also experience high growth rates as the demand for polyolefins, polyesters and polyurethanes keeps on increasing. (4.1 to 4.4% till 2025).
In line with the number of announced projects, the largest refining catalyst consumers in the world are North America (40% of global share in 2018) and the fast-growing Asia-Pacific region (26%). Today, the ‘bright future’ for catalysts is being driven primarily by China, India, and the Middle East.
In the past US demand used to shape the market – catalysts for conversion of heavy crude into lighter products, e.g. Diesel production. However, today a number of initiatives in Europe and other regions are being implemented restricting the use of diesel-fueled cars and therefore the focus catalyst production has shifted to other options: i.e., recently in the CIS region the most requested processes for licensing have been those with higher on-purpose olefin yields. The highest demand is expected for catalyst cracking and hydroprocesses.
Refining catalyst growth factors in different regions

FCC – The Most Popular Catalytic Process
The fluid catalytic cracking (FCC) process is a well-known refinery technology that has been implemented for decades and has evolved to be able to process different feedstock blends, sustain optimal working parameters and stability of gasoline quality and yield. The FCC is a mature technology, but there remains a number of projects under development or planned, especially in the abovementioned regions – some forecasts say FCC catalyst market will value over $3 bln by 2025, currently the share of FCC catalyst is close to 50% of all refining catalysts.
The International Maritime Organization (IMO) regulations (that have come into effect in January 2020) will significantly increase low-sulfur fuels demand post-2020 – this will mean a foreseeable surge for FCC catalysts as refineries aim to maximise middle distillates.
Zeolite catalysts account for around one third of all catalyst currently in operation. Enzymes & bio-catalysts account for nearly 20% of global sales – largely thanks to significant growth in Bio-Refineries, and the increased importance of clean process chemicals for the industry.
The most valuable catalysts are platinum- and palladium containing catalysts – these are used in isomerisation, reforming and hydrogenation processes. – The sales of precious metals catalysts account for an important slice of revenue for catalyst suppliers in ME, Europe and Russia.
Refining-petrochemical integration: influence on the refining catalyst demand

What Benefits Can the Latest Catalysts Bring?
Each new Catalyst that is commercialized is looking to improve operation and results – this means providing:
- longer catalyst cycle lengths;
- higher selectivity;
- optimized activation;
- stable &reliable operation;
- ease of regeneration options;
- lower energy consumption;
- efficiency in certain conditions (i.e. low temperatures, high pressure, water, sulphur & metal content);
- simple process scheme;
- feedstock processing flexibility.
Competition vs. Cooperation
The Catalyst market is defined by high levels of competition and predominantly a corporate organization form – this kind of business requires a developed scientific and technical platform as well as long-term investment into innovative developments, R&D and catalyst testing, etc.. Another core factor of competitiveness is strong brand identity that secures product credibility.
To ensure global market positions catalyst providers have in the past developed partnership with competitors, feedstock suppliers, consumers, and independent R&D organizations – in this area Haldor Topsøe has been one of the leaders for many years. The role of strategic alliances in stimulation of innovation activity is great as is allows partners to consolidate resources, exchange information and allocate risks efficiently.
Albemarle has been cooperating with Axens – on isomerization catalysts. The Criterion catalyst brand has recently totally merged with the Shell Corporation and will support their licensed technologies both in-house and to external customers. They have been also working with Zeolyst International – feedstock suppliers, which is a wise strategic decision that is to bring long-term benefits to both parties (and BASF – largest global chemical company – chose Sumitomo Metal Mining to optimize catalyst feedstock costs in the future).
It is critically important to be ready and flexible in regards to feedstock market volatility (especially metals used for catalyst manufacturing) and to supply tailored catalysts to meet client specific project demands.
An example of a collaborative success story, PTTGC jointly with Honeywell UOP developed a strategy to ensure the right catalyst selection – this strategy helped:
- Maximize distillate yield;
- Provide Flexibility to process special feeds;
- Increase naphtha yield;
- Improve diesel quality;
- All resulted in increased margin to the satisfaction of the client.
All leading refining catalyst producers have opened representative offices and branches in strategic markets like Asia and the ME – this allows to maintain close cooperation with clients, and in some cases helps to optimize transportation outsourcing costs.
This is not always the case as catalyst plants and catalytic technology R&D centers are not always physically integrated into refining and petrochemical clusters - for most part catalyst manufacturing is done ex-situ & abroad. Some countries are currently looking to implement catalyst import-substitution programs.
Local Production – Is It Viable?
In 2019 the top four catalyst companies account for over 80% of the market share, they have a strong presence in strategic countries and regions such as China, India, and ME. This is because there is good accessibility to raw materials in these regions, thus reducing the outsourcing and transportation costs.
Prominent companies in the market own their range of brands, alternatives are not readily available and this enhances the growth prospects of suppliers. But since the number of oil refineries exceeds the number of manufacturers, the market is not essentially led by customers. This is partly a reason why some O&G companies look into manufacturing of their own catalysts for certain processes.
Russia also constitutes a strategic market for catalyst suppliers – in recent years we have already seen Chinese investments in several key O&G integrated companies (i.e. SIBUR). The catalyst sector will also see the same trend and investment from China is expected. Today the market in Russia is dominated by the leading 9 international suppliers (Axens, ART/Grace, ExxonMobil, Albemarle, BASF, Shell, UOP, Haldor Topsoe and Johnson Matthey) – for major refining processes share of import catalyst varies from ~50 to 90%. Russia plans to decrease this level by developing further its own catalyst business. Unlike the global market, in Russia there are several small-scale independent plants that supply certain types of catalysts. The size of the market itself is relatively small (In 2020 one-time catalyst charge at all local hydroprocessing units – over 130 – will reach 21 ktons, till 2030 the growth is expected at rate +25% per annum). Russian majors – Gazprom neft and Rosneft – along with local catalyst company KNT Group plan to increase production of FCC, HD and isomerization catalysts over the next few years, some types have already been successfully tested and put into operation in certain plants. According to Rosneft’s estimates (largest refining catalyst consumer with 1/3 market share) refining catalyst market in Russia has a potential growth of at least 50% to reach 31 thousand tonnes per year in 2030.
An interesting case of Gazprom neft shows consistent dedication to decrease import dependence on a number of process catalysts, focusing again on FCC. In 1965 a local Russian FCC catalyst manufacturing plant was started up, in 2003 they introduced an ultrastable zeolite (+1.0 RON & 1.5% gasoline yield), 2012 – bi-zeolite (+1.5 RON), 2016 – another brand (+3.7% gasoline yield), in 2020 a brand that provides +4.5% gasoline yield is about to be launched. They trialed a new catalyst at their own unit and got positive results including $4 mln. annual margin uplift. An additional large catalyst plant was put into construction late last year and will look to increase significantly corporate capacities for local catalyst production. We see that with these small steps a company can make a significant change on the local market.
Overview:
- Implementation of all announced projects of construction and expansion of catalyst production in Russia by 2020 will allow to fully cover the demand for most of refining catalyst;
- Key issues:
- Lack of experience in modern catalyst production projects implementation
- Quality of produced catalysts to meet international standards and aftersales technical support
- Significant surplus of production capacities over domestic demand including planned regeneration capacities
- Crucial lack of petrochemical catalysts namely in polymerisation, Gas-phase oxidation, Liquid phase oxidation;
- Targets for Domestic Catalysts for 2020 are ambitious but real progress has been made on the different types of catalysts. Challenge is to continue and build on this progress of import substitution.
In Indonesia, Pertamina, put in place the process of developing naphtha HT catalyst technology t- this took about 6 years in total: internal evaluation in R&D (laboratory scale and joint study), evaluation in business development (pilot plant production and testing), evaluation from the technology viewpoint (production at commercial scale in cooperation with another company and then at own unit), strategic and economic evaluation (commercialization of Pertamina catalyst which can be used at 7 proprietary company’s units and also sold to other enterprises).
These examples show that with certain effort and in collaboration with experienced companies and study centers a large oil company can successfully develop a substitute for certain products and/or technologies to have best-tailored alternative, although this path usually takes longer and is more investment intensive than traditional routes.
Catalyst Management Helps Boost Efficiency
Effective catalyst management helps reach higher levels of operational excellence, thus meeting margin improvement targets.
A couple of specific example can help prove this statement: ADNOC implemented a Refining Catalyst Management program, with the objective to optimize the company’s catalyst inventory (5400 t, ~100 references) and at the same time reducing costs and improving performance. One of the main findings was spent catalyst treatment strategy:
- disposal of spent catalyst means 5% additional cost (OPEX)
- recycling – 5-10% saving
- reutilization and reactivation – up to 75% saving
The second example comes from Petronas – Petronas put effort into optimizing Catalyst Bed conditions to achieve best in class reliability performance: without disclosing technical details, we learned that they managed to increase process reliability of hydrocracking complex from 91% to 99% in only 3 years and in parallel reduce losses significantly (from 10 kte and $10 mln to 1 / 1, accordingly).
According to analysis, possible margin increase via optimized catalyst system is significant:
Hydrocracking
- 1-2% volume gain (basis 50,000 bbl/day)
- Margin uplift 10-15 $/bbl
- As a result, up to $5.25 mln. margin increase
Reforming
- 1% volume gain (basis 40,000 bbl/day)
- Margin uplift 0.75-1.3 $/oct-bbl
- Up to $6.37 mln. margin increase
Conclusions
The demand forecast for refining catalysts is expected to grow supported by the implementation of stronger fuel regulations and increasing motor fuel consumption in the developing markets.
Petrochemical catalysts market will be growing due to increase in petrochemical products consumption.
Refining-petrochemical integration is an additional factor that will increase demand for a number of specialised refining catalysts.
There is a number of emerging refining and petrochemical catalytic technologies; their further development and implementation could also significantly change the catalyst landscape.
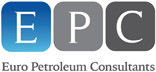
Published by:
