In our industry today, when looking at constructing new refining and petrochemical complexes or revamping existing plants, investors focus their primary attention on refining processes that help increase conversion and petrochemical processes aimed at obtaining a variety of final products (plastics, rubber, etc.).
These types of processes, more often than not, mean aggressive and super-aggressive operating conditions - high pressure and temperature that result in specific requirements for main process equipment. Since the cost of such equipment constitutes up to 40% of the total cost of the project, and the manufacturing time for some items can be over 20 months, the importance of the correct and timely placement of orders and proper quality control over the course of production is essential.
Unfortunately, in some cases customers underestimate the role of independent quality control during manufacturing – this oversight can lead to some risks and dangers such as:
- Deviation from the specifications in terms of dimensions,
- Issues with the Finished Product characteristics,
- Non-compliance with material and design specifications,
- Incompleteness (constructive components, spare parts, final documentation, certificates, etc.) upon shipment,
- Careless preparation for shipment (no flange plugs, violation or absence of protective packaging, etc.),
- The inability to ensure the normal operation of the equipment after installation.
Under unfavorable circumstances, correcting some of these deviations may cause important delays in the delivery of equipment and, therefore, a delay in the execution of the unit construction --- Projects can be delayed by up to several months.
A systematic & logical approach to the quality control of equipment manufacturing can significantly reduce these risks and their negative effect.
A prime example is an EPC-contractor’s typical approach to equipment manufacturing control - EPC-contractors, who are financially responsible both for project budget and schedule, and for the quality of supplied equipment, fully control all stages of items manufacturing.
In this case, participation of the EPC-contractor’s representatives starts with pre-inspection meeting organised by the supplier, and then finalized through the Inspection and Test Plan containing the full list of inspections, and also determined involvement of each controlling party in every inspection.
There are three main generally accepted degrees of criticality in equipment inspection:
- R (Review) – documentation control (certificates, test reports, etc.),
- W (Witness) – witnessing of tests conducted by the manufacturer’s personnel, in the case of unsatisfactory results of which production continues,
- H (Hold) – witnessing of tests conducted by the manufacturer's personnel, in the case of unsatisfactory results of which production is suspended.
The number of parties that control the course of the equipment manufacture can reach four:
- Representatives of the supplier’s quality department,
- Representatives of ЕРС-contractor,
- Representatives of the process’ Licensor,
- Representatives of the end-customer.
The degree of criticality for each party is different. For instance, for representatives of the supplier’s quality department, all inspections and tests are H-critical. Representatives of the EPC-contractor also participate in all inspections specified in the Inspection and Test Plan for critical equipment, but H criticality is assigned only for the most critical inspections, for example, hydraulic tests of tanks and vessels.
Representatives of the end-customer often take part only in the most critical inspections usually carried out at the end of the manufacturing cycle of a machine or equipment, for example, running tests of the pump unit assembly. At these stages, the degree of criticality for the final customer is W, in rare cases - H. In all other inspections of the critical equipment supplied by the EPC-contractor, the end-customer either does not fully participate or only checks the test reports, which corresponds to the criticality R.
Table 1 shows a typical Inspection and Test Plan for a centrifugal pump, which shows the scope of inspections by the EPC contractor and customer under the EPC contract.
Control points | Vendor | ЕРС-contractor | Customer |
---|---|---|---|
Before Manufacturing | |||
Vendor documentation review and approval | H | H | R |
Pre-inspection meeting | H | H | R |
Inlet materials certificates checking | H | W | R |
Visual inspection of inlet materials | H | W | |
PMI | H | H | R |
During Fabrication | |||
Casing Visual Inspection | H | W | |
Impeller visual inspection | H | W | |
Casing hydrotest | H | H | |
Casing NDT results control | H | H | R |
Impeller Dynamic Balance Test | H | H | R |
Impeller NDT results control | H | W | |
Impeller overspeed test | H | W | |
Impeller NDT results control after overspeed test | H | H | R |
Pump Assembly inspection | H | W | |
Mechanical Running Test | H | H | W |
Strip Down Inspection | H | H | |
Performance (or NSPH) test | H | H | W |
Final inspection | H | H | W |
Packing and marking inspection | H | H | |
Sub vendor inspection (motor) | |||
Performance test | W | W | W |
Final inspection | H | W | |
Sub vendor inspection (Control panel) | |||
FAT | H | W | |
Final inspection | H | W |
When it comes to Refining & Petrochemical complexes, the quality of all equipment, components, structures and materials is subject to many regulations and standards.
Clearly defined and fully implemented Quality assurance and quality control help ensure compliance with all contractual specifications, mandatory regulations and quality standards.
This is especially true with critical equipment in severe operating conditions – we have seen that these pieces of equipment make up a significant slice of the total cost of the project, and the therefore it is essential to implement a robust and reliable approach to Quality control through all stages of manufacturing and implementing. The overall success of the project may depend on it. This should be considered as a key component of project Risk management.
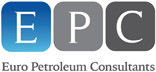
Published by:
