Increasing the depth of conversion and reducing heavy residue volume is a global trend in oil refining caused by a global decrease in fuel oil consumption. The tendency is not something new - since the end of the ‘70s, global consumption of fuel oil has been on a downward trend. Of course, the situation varies in different regions. In Europe, the maximum was reached in the early ‘70s, in FSU it was at the end of the ‘90s - the last years of the USSR. In Asia Pacific region the peak was in the late ‘70s, and then the region had ten years of decline in fuel oil consumption followed by ten years of growth caused by extensive economy growth in such countries as China, South Korea, Singapore and Thailand.
Nevertheless, from 2000 to 2016, the annual average global growth rate of fuel oil consumption was < 1.6%, and the Middle East is the only region with sustainable growth. The reason for this growth is the booming economy of the region – according to the World Bank, during the specified period, the GDP of the MENA region has increased by more than three times. Regarding fuel oil consumption, this primarily affected the growth of maritime navigation in the region, hence seeing an increased consumption of bunker fuel with an average annual growth rate of about 5% per year. As a result, from 2000 to 2016, fuel oil consumption as international marine bunker fuel increased from 13 million tons per year to 28 million tons per year.
Meanwhile, it is common knowledge that in 2020 maritime navigation is in for a revolutionary shock, comparable to that of transiting from coal to fuel oil at the beginning of the 20th century. Such are the new requirements of the International Maritime Organization (IMO) on harmful emissions from ships. Today, there is no shortage in forecasts on how these requirements will affect shipping and which of the possible solutions – installing scrubbers on ships, switching to low-sulphur fuel oil, accelerated development of alternative fuels such as LNG, methanol, electricity, etc. – will be most prevalent. However there is one thing most experts agree on – these requirements will lead to a reduction in the consumption of fuel oil with sulphur content above 0.5%.
Another significant application for fuel oil in the Middle East – electricity and heat generation – also saw a consumption increase in the period reviewed. Yet, this growth was significantly lower than the regional economic growth, only 1% per year. Besides, the global generation trend is to displace oil-based fuels with the more environmentally friendly alternatives such as natural gas and renewable energy.
While fuel oil supply-demand balance in the Middle East has been fairly stable in the past few years, the trends and threats we mention above force the local refiners to focus on ways to minimise fuel oil production at their facilities. Some success was already achieved in the period from 2000 to 2016 when fuel oil yield decreased from 30% to 25%, but this is still significantly higher than that of competitors from other regions - North America, Western Europe and the Asia-Pacific Region.
Currently, there is a whole range of commercially proven deep conversion technologies such as delayed coking, visbreaking, deasphalting, residual fluid catalytic cracking (RFCC), ebullated bed hydrocracking, slurry processing, etc., but selection of an optimum configuration strongly depends on specific aims of the refinery – maximising gasoline or diesel production, integration with petrochemical business, production of niche products such as bitumen, lube or petroleum coke, power generation, etc.
Below are just a few examples of how Middle East refiners are increasing the depth of conversion.
In terms of prevalence, delayed coking is the most popular process to convert oil residues in the world, and the Middle East is no different.
On September 2, UAE’s Abu Dhabi National Oil Company (ADNOC) announced that it successfully commissioned a specialised delayed coker unit (DCU) as part of its Carbon Black and Coker Project. The new unit will enable ADNOC’s refining business to recover highly specialised and valuable grades of carbon black and calcined coke – the compounds used in tyres and rubbers, and the steel and aluminium industries, respectively. Through its Carbon Black & Coker Project, ADNOC Refining can produce 40,600 tons of two different grades of carbon black per year, and 430,000 tons of anode grade calcined coke, which is low in sulphur and metals. Borouge, a joint venture between ADNOC and Austria’s Borealis, makes extensive use of special carbon black grades across a range of products, including high-pressure water and gas pipes, steel pipe coatings and linings, and standalone piping.
Another example of a DCU project is Oman’s Duqm Refinery and Petrochemical Industries Company (DRPIC). The company is constructing a 230,000 bpd refinery that will be able to process a variety of crudes. As a deep conversion complex, the company chose a 52,000 bpd DCU licensed by Wood. The completion of the project is scheduled for the third quarter of 2022.
The global demand growth for petrochemical products became a driver for strengthening the integration between oil refining and petrochemistry even in the Middle East - a region that traditionally used gas as a feed for petrochemical plants.
Kuwait National Petroleum Company (KNPC) is developing a new multi-billion grass root refinery in the Al-Zour area, 90km south of Kuwait City. Known as the Al-Zour Refinery project (ZOR), it will be able to process 615,00 bpd of Kuwait’s crudes and produce Euro V motor fuels and petrochemicals products such as paraxylene and propylene. Focusing on refining/petrochemical integration, the project includes a 50,000 bpd RFCC complex with ethylene and propylene recovery licensed by Honeywell UOP. In January, KIPIC confirmed that all five packages of the integrated complex are proceeding in line with the original schedule, with all packages due to be completed by yearend 2019 and initial refining units still on track for startup in May 2019.
Another factor that predetermines the configurations of deep conversion complexes is the development of residue hydrocracking technologies.
Bahrain Petroleum Co. (BAPCO) is implementing Bapco Modernisation Programme (BMP) that aims to reduce fuel oil yield to 7% vol. from 15-16% vol. now. As a deep conversion solution for its 267,000 bpd refinery at Sitra, the company chose LC-FINING residue hydrocracking technology licensed by Chevron Lummus Global (CLG). The capacity of the unit is 65,000 bpd and the Sitra modernisation project is scheduled to be completed in 2022.
The examples above are just a few of the projects that are being implemented in the Middle East aimed at curbing fuel oil production in line with global trends in the development of the refining industry. Today the licensors have a variety of technologies to offer the refineries, and each refinery can find a perfect fit for its operating and investment strategies.
To find out more about modern deep conversion technologies, do not miss the opportunity to attend EPC’s focused event BBTC MENA 2018 – Bottom of the Barrel Technology Conference, taking place on 3–4 December in Bahrain, www.bbtc-mena.biz
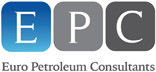
Published by:
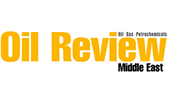