HAZOP studies are one of the most widely used hazard identification methods and have found applications in many aspects of both the oil and gas industries.
Many potential problems can be identified by the examination of the new, modified or existing designs, the procedures and the operations; all using the systematic and structured approach of HAZOP. Maximum effectiveness in HAZOP study requires skilled leaders as well as experienced and committed team members.
A very powerful instrument that could be used to ensure safety levels in the organisation is a combination of HAZID and HAZOP. HAZID (Hazard Identification) process should be ongoing to ensure existing hazards are known, potential new hazards identified, abnormal operations & troubleshooting monitored, and any incident or near-miss recorded and analysed.
HAZID approach should consider all operating modes of the facility, and all activities that are expected to occur, also be dynamic to stay ahead of any changes in the facility and integrate human and machine/system interfaces together with engineering issues.
The process of HAZID planning and execution requires a number of steps, including preparation, defining boundaries & providing system description, dividing the plant into logical groups, reviewing P&IDs and analysing process schematics.
HAZOP is mostly used for identifying hazards and operability problems and can be applied to operating process plants and to plants in various stages of design. The plant to be studied is defined at the beginning of the HAZOP typically using a P&I Diagram to clarify the battery limits and interfaces.
The HAZOP team is comprised of a leader (or Chairman) who defines the nodes to be reviewed (i.e. dividing the process/plant into segments), he or she asks questions of the team, a recorder who records the discussion, points made, actions required and team members who represent the key disciplines involved in the facility, such as:
- Process Design
- Instrumentation & Control
- Equipment Specialists (Fired Heater, Compressors, etc)
- Operations
- Safety & Maintenance
The review takes a question and answer approach using guidewords to search for deviations from design intent or failure modes of the plant. Each section is examined critically to understand the design intent of the facilities between nodes selected by the leader. At the end of the HAZOP a list of recommendations should be provided. These need to be allocated for review and implementation with a budget and timetable. A template or software package can be used to generate the documentation of the HAZOP review.
HAZOP studies should be carried out at the following stages of a plant’s life: during initial design phase, once the P&I has been fully defined; both normal operations and start-up and shutdown procedures; any significant plant modifications; on a routine basis - minimum every 5 years.
The training of staff is a very important aspect if the HAZID/HAZOP results are to be successfully implemented. Both managers and key specialists involved in production activities should be aware of process hazards and associated risks, tools and procedures to comply with requirements – and most importantly should pass on this knowledge to all co-workers.
The training of staff is a very important aspect
With companies trying to get more out of existing assets this could have a potential impact on safe operations. It is therefore important for companies to perform hazard identification, scenarios of development and assessment of potential consequences, which under certain conditions could cause injury to personnel, population, environment and equipment.
The analysis process aims to identify deviations in process security during operation, which may compromise the performance of the work in the field of industrial safety, as well as the total working efficiency and reliability of equipment.
Typical subjects of the study include:
- Existing scheme/technology of the facility in operation
- Technical regulations for the operation
- Emergency response plans
The report should contain at least the following items:
- Description of process
- Methodology
- Points of HAZOP analysis
- Lessons learned from HAZOP analysis
- Matrix criticality/probability of occurrence of event
- Recommendations for priority of implementation of measures
- List of typical design errors with description
- Documents of analysis
- Other sections according to technical assignment to execute HAZOP
HAZOP Reviews on Existing Facilities
Companies now recognise the important need to investigate the safety features of existing plants taking into account recent accidents in offshore facilities and also in refineries.
To perform these types of reviews it is important to have very experienced specialists to lead and carry out such reviews.
The following approach is typically used:
- Review Drawings such as piping and instrumentation (P&Ids), process diagrams (PFD's), working process schemes & assemblies, piping and instrumentation, engineering support systems;
- Check Conformity of the constructed facilities to the original design solutions for the process technology;
- Review General and situational plan with indication of zones of the impact of explosions, fire and toxic damage to assess the specific risk factors and the possibility of damage to personnel, population, environment;
- Review Engineering systems: pressure relief system, drainage, inert gas, gas contamination and fire detections system, fire-fighting system, power supply, protective earth & lightning protection, crash protection system PAZ, warning & alarm systems;
- Identify potential deviations & causes of source of danger in the unit;
- A study of each deviation hazard source;
- Using the key parameters of the technological process;
- Determination of the consequences of each deviation of danger source;
- Determination of the adequacy of the protection measures provided by the design solution of the investigated object (ie protection measures provided by the project, including preventing or signaling about the deviation); and
- Security (i.e. deviation can actually lead to an accident, and injuries or fatalities);
- Environmental pollution (emissions of hazardous substances, pollution);
- Operation of object (disturbance of operating regime, shutdown of production, losses of the enterprise);
- Definition of responsible persons to execute each recommendation (the operating organisation and/or Design Company); and
- Decision-making on the degree of criticality (high, medium and low) of recommendations, the definition of risk is carried out depending on the impact to personnel connected with the probability of occurrence of an event according to the approved risks matrix.
And then in order to identify and assess compliance of existing facilities with requirements imposed on process operations, a site visit (visual inspection of the facility) is required along with analysis of relevant drawings & schemes.
As mentioned previously, in today’s industry companies are looking to getting the most out of existing assets – this can present potential issues with regards to maintaining safe operations and therefore reviewing and monitoring certain key parameters is essential to the good and safe running of a plant. To conclude we can say that carrying out rigorous HAZOP studies is a key step to help ensure future safe operations.
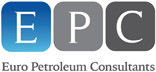
Published by:

